Le système de manutention des solides en vrac améliore les opérations de calandrage
MEXICO CITY — L'un des plus grands transformateurs de plastiques de la ville de Mexico a rationalisé la manutention des matériaux, amélioré la qualité des processus, créé un environnement de travail plus sûr et affecté plus efficacement sa main d'œuvre en installant un système de déchargement de Big Bags avec convoyage pneumatique et à vis flexible.
Oplex S.A. de C.V. calandre des feuilles de polychlorure de vinyle (PVC) pour des applications telles que les bannières publicitaires, les housses de sièges et revêtements de portières automobiles, les auvents, les rideaux de douche et le cuir synthétique. L'entreprise produit des feuilles sur deux lignes de calandrage qui reçoivent les composés de PVC à partir d'un système central de mélange par lots. Les travailleurs chargeaient manuellement des sacs en papier de 25 kg de résine de PVC et de carbonate de calcium (CaCO3), les composants solides des formulations, dans un mélangeur et ils utilisaient un système de convoyeur conçu spécialement par l'entreprise pour ajouter des composants liquides — plastifiants, stabilisants et lubrifiants.
Carlos Barra, directeur des opérations chez Oplex, affirme que le chargement manuel créait des problèmes, notamment en matière de contrôle de la qualité. Oplex mélange six lots par heure — 144 par jour — pesant chacun 200 kg, y compris les additifs liquides. Avec un lot mélangé et déchargé toutes les 10 minutes, les travailleurs devaient se dépêcher, ce qui entraînait des erreurs. Il n'était pas inhabituel pour eux d'oublier quelle quantité de produit avait été ajouté à un lot, note M. Barra. Et comme les sacs étaient ouverts avec des couteaux, des particules de papier tombaient parfois dans le mélange. Le travail était répétitif, ce qui créait un risque de blessures lors du transport les sacs jusqu'à la station de mélange. Les sacs vides devaient également être collectés et éliminés, ce qui augmentait les coûts de production.
Oplex a décidé d'automatiser le mélange de résine de PVC avec un système de déchargement de Big Bags, estimant que cela permettrait non seulement d'améliorer la qualité des lots, mais aussi d'utiliser plusieurs douzaines de sacs en vrac de 700 ou 1 000 kg au lieu de centaines de sacs de 25 kg. Un système automatisé créerait également un environnement de travail plus sûr en réduisant la quantité de travail manuel nécessaire au chargement et au mélange des lots.
L'entreprise a développé un cahier des charges pour un système de manutention de matériaux de PVC. L'une des exigences était que l'équipement devait être compatible avec un contrôle logique programmable et le logiciel Oplex développé en interne. Le carbonate de calcium serait toujours chargé à la main à partir de sacs de 50 kg car il n'est pas disponible en Big Bags. Oplex voulait cependant installer une trémie plus efficace et une station de mélange d'additifs pour CaCO3.
La première partie du système est une station de vidange de Big Bags de la série BFC de Flexicon. La station de vidange est équipé d'un chariot-palan électrique monté sur une poutre en porte-à-faux qui soulève des sacs pesant jusqu'à 1 450 kg pour les placer sur un cadre en acier au carbone à environ (6 m) de hauteur.
La résine de PVC s'écoule du sac dans un tube télescopique TELE-TUBE™ qui est fixé manuellement à la manchette du sac à l'aide d'un collier de serrage SPOUT-LOCK™, ce qui crée une connexion étanche à la poussière. Le tube se soulève et s'abaisse grâce à une commande pneumatique, il applique une tension continue vers le bas pour allonger le sac et maintenir la manchette tendu, ce qui empêche la manchette de créer des renflements (des poches mortes) ou de s'accumuler à l'intérieur (créant des restrictions d'écoulement), pour une évacuation complète. Un évent de collecteur de poussière monté sur le cadre de la station de vidange aide à empêcher la poussière de s'échapper dans l'usine. Cela permet non seulement de protéger la santé des travailleurs en réduisant les particules en suspension dans l'air, mais aussi d'améliorer la propreté de l'usine et de réduire le risque de contamination du produit par d'autres particules.
Une vanne de réglage de débit POWER-CINCHER™ à commande pneumatique permet à l'opérateur de refermer les Big Bags partiellement vides si besoin. Quatre barres de serrage de forme elliptique se ferment concentriquement autour de la manchette de déchargement du sac de manière à se chevaucher afin d'éliminer complétement l'écoulement du matériau.
Oplex se trouve dans un vieux bâtiment avec peu d'espace horizontal, de sorte que les opérations sont réparties sur plusieurs étages. Un système pneumatique par aspiration transporte la résine de PVC des Big Bags vers un filtre de réception au troisième étage de l'usine. Une trémie intégrée à la station de vidange de Big Bags dirige la résine de PVC vers une écluse rotative à passage direct, qui mesure la quantité de matériau déchargée dans l'une des deux conduites de convoyage pneumatique de 7,6 cm de diamètre, le transportant sur 60 m jusqu'au filtre de réception de 91,4 cm de diamètre situé au-dessus du mélangeur. La station de vidange de Big Bags est équipée de pesons pour permettre au contrôle logique programmable de recevoir les données de perte de poids au fur et à mesure que le matériau se vide de la station de vidange. Ceci permet au contrôle logique programmable de contrôler l'alimentation du convoyeur pneumatique afin que le poids requis de résine de PVC soit acheminé vers le filtre de réception, puis passe dans une goulotte avant de finir sa course dans le mélangeur. Les deux conduites de convoyage pneumatique séparées empêchent la contamination croisée lors de l'acheminement de produits différents.
Au deuxième étage, Flexicon a installé une trémie vide-sacs avec collecteur de poussière pour le chargement du CaCO3. Les matériaux provenant de la trémie vide-sacs sont transportés vers une petite trémie de pesée au troisième étage par le convoyeur à vis flexible BEV-CON™ de Flexicon. Une vis flexible en acier inoxydable, conçue pour déplacer des matériaux difficiles à manipuler, tourne dans un tube en plastique de 8,9 cm de diamètre et de 9 m de long, à une inclinaison de 45 degrés. La vis s'auto-centre également lorsqu'elle tourne, offrant ainsi un espace entre la vis et la paroi du tube pour éviter le broyage du matériau. Le convoyeur est alimenté par un moteur de 3,7 kW à l'extrémité de déchargement où le CaCO3 entre dans la trémie de pesée par l'intermédiaire d'un adaptateur de transition. Les pesons situés sous la trémie de pesée permettent de mesurer d'atteindre des poids précis de CaCO3. De la trémie, le lot pesé est acheminé jusqu'au mélangeur en passant par une vanne guillotine.
«La précision des opérations de chargement, de pesée et de mélange du système automatisé a amélioré la qualité et la répétabilité du produit en general», explique M. Barra. «De plus, en permettant l'utilisation de Big Bags au lieu de sacs de 25 kg de PVC, le système automatisé de manutention des matériaux réduit l'espace au sol nécessaire pour le stockage des matériaux».
Du troisième étage, la résine de PVC et le CaCO3 s'écoulent (par gravité) du filtre de réception et de la trémie de pesée, respectivement, jusqu'au mélangeur au rez-de-chaussée où les liquides sont ajoutés. Après la préparation du lot, une quantité précise est vesée dans deux machines de mélange. Un mélangeur, un malaxeur Buss, traite jusqu'à 1 200 kg par heure. Le composé est déchargé dans un broyeur à deux cylindres pour l'aération, puis dans une calandre où il produit des feuilles de 1,8 m de largeur. L'autre ligne utilise un mélangeur Banbury qui traite le composé à la même vitesse et le décharge dans un moulin à deux cylindres et un extrudeur-filtre, puis dans une deuxième calandre, qui produit des feuilles de 1,6 m de largeur.
M. Barra note qu'un facteur important dans la conception du système pneumatique a été l'altitude de Mexico: À 2 240 m au-dessus du niveau de la mer, l'air se raréfie. Flexicon a dû ajuster le système de convoyage pneumatique pour maintenir de bonnes performances et s'assurer que les ventilateurs, qui refroidissent les moteurs, génèrent suffisamment de flux d'air pour être efficaces. «Les résultats de Flexicon dans ces domaines, ainsi que dans l'ensemble de l'installation, se sont avérés très satisfaisant», explique M. Barra.
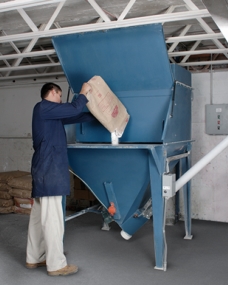
En savoir plusUn ouvrier charge l'additif de carbonate de calcium dans la trémie vide-sacs au deuxième étage de l'usine Oplex. Le convoyeur à vis flexible, situé à droite, transporte l'additif sur 9 m jusqu'à une trémie de pesée au troisième étage.
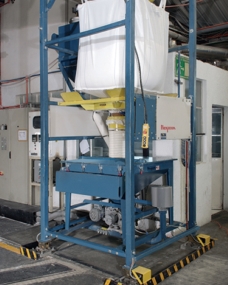
En savoir plus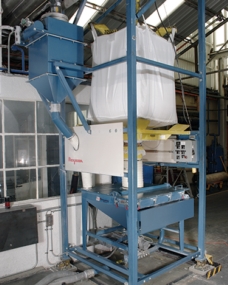
En savoir plusOplex a installé une station de vidange de Big Bags de la série BFC de Flexicon pour améliorer la qualité et la productivité de ses opérations de mélange de PVC. Les caractéristiques comprennent une poutre en I et un palan en porte-à-faux, un collecteur de poussière BAG-VAC, des activateurs de sac FLOW-FLEXER™ sous le sac pour assurer le bon écoulement du matériau, un tube télescopique TELE-TUBE et un collier de serrage SPOUT-LOCK à l'interface de la manchette du sac, une trémie et une écluse rotative commandée par un contrôle logique programmable.
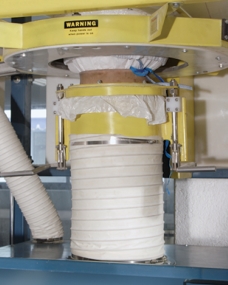
En savoir plusAu niveau de l'interface de la manchette du sac, un collier de serrage SPOUT-LOCK crée un joint étanche à la poussière tandis qu'un tube télescopique TELE-TUBE maintient une pression constante vers le bas au fur et à mesure que le sac se vide et s'allonge, ce qui favorise un déchargement complet.

En savoir plus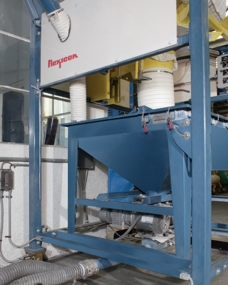
En savoir plusSous la trémie du cadre de la station de vidange de Big Bags, une écluse rotative à passage direct mesure la quantité de résine de PVC versée dans deux conduites de convoyage pneumatique.
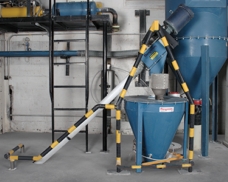
En savoir plus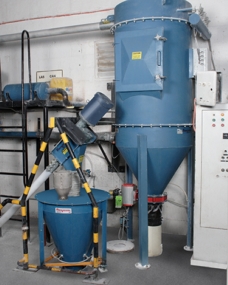
En savoir plusLe PVC provenant de la station de vidange de Big Bags est transporté pneumatiquement vers un filtre de réception et une trémie de 91,4 cm de diamètre au troisième étage de l'usine Oplex. Le convoyeur à vis flexible vide le carbonate de calcium dans la petite trémie de pesée. Les deux ingrédients sont ensuite acheminés par gravité jusqu'au mélangeur à l'étage en dessous.
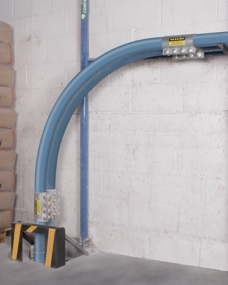
En savoir plus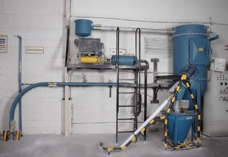
En savoir plusDeux lignes de convoyage pneumatiques transportent le PVC de la station de vidange de Big Bags au rez-de-chaussée jusqu'au filtre de réception au troisième étage de l'usine Oplex.
T-0944