Pigments d'encre pour impression offset et d'encre hélio pesés par des systèmes de déchargement de Big Bags
SUSSEX, WI, USA — Depuis ses humbles débuts en 1971, avec une presse louée et une reliure empruntée dans une usine de menuiserie abandonnée à Pewaukee, Wisconsin, Quad Graphics (www.qg.com) est devenu un fournisseur mondial de communications écrites et numériques évalué à 4,8 milliards de dollars. Aujourd'hui, l'entreprise compte environ 24 500 employés répartis sur environ 60 sites en Amérique du Nord, en Amérique latine et en Europe.
L'une des clés du succès de l'entreprise est l'accent mis sur l'intégration de services, allant de la gestion des données et du développement créatif jusqu'à l'imagerie électronique, la production imprimée et la distribution. Cela inclut la fabrication de ses propres encres d'impression — non seulement offset et hélio, mais aussi d'encres métalliques et fluorescentes et d'encres invisibles utilisées comme marquages de sécurité. L'entreprise produit même des encres phosphorescentes à base d'un mélange exclusif de vernis et de cristaux qui absorbent et stockent la lumière ultraviolette (UV) et libèrent une longueur d'onde spécifique (couleur) selon le type de cristal utilisé.
Le département de recherche chimique/technologie de Quad Graphics est responsable de toutes les facettes de la production d'encre, de la R&D au mode de préparation et à la fabrication. Les encres offset respectueuses de l'environnement avec un contenu renouvelable allant jusqu'à 27 % sont fabriquées dans une usine entièrement intégrée à Hartford, WI, tandis que les encres hélio à base de solvants sont produites dans une usine de fabrication située à Martinsburg, WV. Dans les deux installations, le pigment pour la production de diverses couleurs est reçu dans des Big Bags pesant de 272 à 907 kg chacun, qui sont vidés et transportés dans des cuves de mélange en utilisant un système de déchargement de Big Bags de Flexicon.
Encres Offset conçues pour être durables
En 1982, le département de recherche chimique/technologie a commencé à préparer et à fabriquer ses encres offset EnviroTech en utilisant des matériaux de la plus haute qualité et des installations de traitement à la pointe de la technologie. «Ces encres ont une teneur en ressources renouvelables, y compris en huiles végétales et en résine de pin, d'environ 27 % — bien au-dessus de la norme industrielle d'au moins 20 %«, a déclaré Charlie Buckett, directeur de la fabrication à l'usine de Hartford.
«L'impression offset se fait avec quatre encres de couleur différentes appliquées selon un motif de points généré de manière photographique», explique M. Buckett. «Les encres, connues sous le nom de CMYK, sont le Cyan (bleu), le Magenta (rouge), le Jaune (Yellow) et le Key (ou valeur, qui représente le noir, la couleur sur laquelle les autres sont incrustées). Le cyan, le magenta et le jaune sont produits à partir de pigments de couleur correspondante et le noir est produit à partir de noir de carbone».
Lors de la livraison à l'installation de Hartford, WI, les Big Bags sont placés sur des stations de vidange de Big Bags Flexicon, une pour chacune des quatre couleurs de pigments. Chaque modèle de station de vidange BFC est équipée d'un palan électrique fixé à un chariot qui se déplace sur une poutre en I en porte-à-faux, permettant aux sacs d'être soulevés du sol et acheminés jusqu'au cadre sans avoir recours à un chariot élévateur.
Les pigments en poudre sont connus pour être difficiles à manipuler, en raison de ses propriétés physiques qui font que le produit a tendance à s'emmagasiner, à former des galette, à s'étaler et à générer de la poussière. Pour faire face à ces conditions, les caractéristiques de conception du système de manutention des matériaux doivent être intégralement pensées et soigneusement sélectionnées. Pour éliminer la poussière et favoriser l'écoulement pendant le déchargement, un collier de serrage manuel SPOUT-LOCK™ est soulevé pneumatiquement par un tube télescopique TELE-TUBE™, ce qui permet à l'opérateur d'établir une connexion étanche à haute intégrité avec la manchette du sac. Le tube télescopique, avec une prise de ventilation de 15 cm de diamètre extérieur pour l'interface avec un collecteur de poussière conçu par le client, maintient une tension constante vers le bas sur le sac au fur et à mesure qu'il se vide ou s'allonge, favorisant le déchargement complet du pigment à écoulement difficile dans une trémie de sol pyramidale de type «T» d'une capacité de 0,25 m3 mesurant 81 cm2 par 107 cm de haut. Les stations de vidange sont construites en acier inoxydable et comprennent une vanne de réglage de débit POWER-CINCHER™ pour réguler le débit et permettre une fermeture sans poussière des sacs partiellement vidés.
À partir de la trémie, le pigment pénètre dans un convoyeur à vis flexible de 975 cm de long, qui utilise une vis flexible en acier inoxydable ayant une géométrie spécialisée pour transporter les matériaux à écoulement difficile. Le convoyeur transporte le pigment à une inclinaison de 45 degrés, le déchargeant dans l'un des quatre alimentateurs par perte de poids, chacun étant relié à un réservoir de prémélange de 640 cm de haut situé à environ 716 cm de la trémie, où il est mélangé avec le vernis pour former une boue solide à environ 30 %.
Le convoyeur à vis flexible décharge le matériau en fonction de la quantité de poids perdu. Les pesons sur lesquels la station des vidange est montée, envoient des signaux à un contrôle logique programmable pour activer la vis lorsque 9,1 kg de pigment ont été délivrés dans la trémie, et recommencent cinq fois pour acheminer un total de 45,4 kg dans le réservoir de prémélange.
«Les boues de chaque pigment sont ensuite introduites dans une cuve de stockage avec des compartiments séparés pouvant contenir jusqu'à 4 prémélanges», explique M. Buckett. «A partir de la cuve de stockage, les différentes boues de couleur sont introduites séparément dans des moulins à billes horizontaux, d'une capacité d'environ 200 l chacun, pour réduire la taille des particules et encapsuler le pigment afin de créer la base d'encre finie pour chaque couleur. Divers ingrédients brevetés sont ensuite ajoutés à chaque base pour créer les encres finies».
Les encres hélio nécessitent une manipulation special
Les mêmes pigments qui produisent des encres thermodurcissables à l'usine de Hartford, WI, sont utilisés à l'usine de Martinsburg, WV, pour produire des encres hélio à base de solvants. «Dans cette usine, quatre stations de vidange de Big Bags, chacune équipée d'une trémie vide-sacs auxiliaire manuelle, sont installées au deuxième étage», raconte Glenn Gogin, responsable spécialisé des processus de recherche chimique/technologie. L'opérateur utilise la trémie vide-sacs pour verser un sac de 23 kg d'additifs spéciaux qui sont transportés dans un convoyeur à vis flexible avec le pigment vers une trémie située au-dessus d'une cuve de mélange (une cuve par couleur). Le pigment et les additifs sont introduits par gravité dans chaque cuve de mélange lorsque le procédé l'exige.
Le contenu de chaque cuve de mélange est ensuite acheminé dans une cuve de stockage similaire à celle utilisée dans l'installation de Hartford. Contrairement à Hartford, cependant, l'usine de Martinsburg utilise un concept innovant, qui consiste à peindre chaque station de vidange de Big Bags, trémie, cuve de mélange et autres équipements de l'usine de la couleur correspondant au pigment manipulé.
«Les pigments étant mélangés avec du toluène, un solvant organique volatil et inflammable, les encres finies sont mélangées dans des cuves de mélange antidéflagrantes situées en aval de la cuve de stockage», fait remarquer M. Gogin. «Afin de réduire au minimum les émissions de composés organiques volatils (COV), une salle des machine d'impression hélio conçue comme une enceinte close se situe à l'intérieur de l'usine de Martinsburg. Des tuyaux de grand diamètre permettent de capter la quasi-totalité de l'air chargé de solvants dans la salle des machines d'impression en vue d'une réutilisation. L'efficacité du système surpasse régulièrement la norme de 92 % exigée par l'EPA et à la moyenne de 96,86 % de l'industrie».
Pour les deux systèmes de déchargement de Big Bags, M. Buckett explique: «Nous avons envoyé des échantillons de chaque pigment de couleur à Flexicon pour qu'il les analyse et nous avons précisé les débits d'alimentation requis». Ils les ont pris en compte pour créer le système répondant à ces critères. Le système fonctionne si bien que dans l'usine de Hartford, nous traitons régulièrement environ 72 575 kg de pigment sec chaque semaine avec les quatre stations de vidange de Big Bags sans aucun problème.
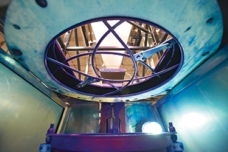
En savoir plus
En savoir plus
En savoir plusUne vanne de réglage de débit POWER-CINCHER™ régule le débit et permet de refermer un sac partiellement vidé en serrant la manchette de manière concentrique.

En savoir plusDans la production d'encres offset, les pigments de chaque couleur de base (par ex. cyan, à gauche et magenta, à droite) sont transférés dans une cuve de prémélange à partir d'une station de vidange de Big Bags BULK-OUT® BFC et d'un convoyeur à vis flexible de 975 cm de long, tous deux de Flexicon.

En savoir plus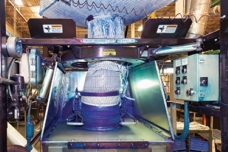
En savoir plusAu niveau de l'interface de manchette de sac, un collier de serrage SPOUT-LOCK™ (à gauche) et un tube télescopique TELE-TUBE™ (à droite) éliminent la poussière et contrôlent le débit. Également à droite, les plaques d'activation de sac FLOW-FLEXER™ favorisent l'écoulement du matériau.

En savoir plusAu départ, les encres offset sont des pigments CMYK (cyan, magenta, jaune, key [noir]). Chaque poudre est transférée par son système de déchargement de Big Bags de la couleur correspondante.

En savoir plus
En savoir plusLes pigments en poudre à écoulement difficile ont tendance à former des galettes, à s'étaler et à générer de la poussière.
Y-0422