Le système de manutention de matière vrac permet de garder une usine d'explosifs propre
BIWABIK, MN — Minnesota Explosives Company fabrique des explosifs en vrac qui sont utilisés pour faire exploser la taconite en petits morceaux, la première étape de la récupération du minerai de fer. Pour produire les composés explosifs, du nitrate de sodium, un matériau solide granulaire, est ajouté à une solution corrosive de nitrate d'ammonium à haute température.
Auparavant, le nitrate d'ammonium était inséré dans une grande boîte ouverte appellee «boîte à boue», où la solution circulait. Un opérateur utilisait un chariot élévateur pour positionner un Big Bag contenant des granulés de nitrate de sodium au-dessus de la boîte à boue et le vider dans la solution.
Cette opération entraînait souvent le bouchage de la pompe et des tuyaux dans la boucle de circulation du récipient. La solution de nitrate d'ammonium débordait de la boîte à boue et s'écoulait sur le sol de l'usine. De plus, il fallait deux opérateurs - l'un pour faire fonctionner le chariot élévateur, l'autre pour surveiller la boîte à boue et arrêter le processus de remplissage afin d'éviter les débordements.
«Nous voulions un système qui élimine le écoulements accidentels de solution», dit Jon King, directeur général des opérations de Minnesota Explosives. L'entreprise a donc remplacé la boîte à boue ouverte par un système de manutention fermé composé d'une station de vidange de Big Bags, d'un convoyeur à vis flexible pour manipuler le nitrate de sodium, et de deux réservoirs d'une capacité de 104 000 kg pour mélanger le matériau avec la solution de nitrate d'ammonium. «À l'exception de certains granulés qu'il faut parfois balayer et mettre dans la trémie, il s'agit essentiellement d'un processus ne nécessitant aucun nettoyage» remarque M. King.
Dans le nouveau procédé, le nitrate d'ammonium liquide est chargé dans deux cuves de mélange isolées qui sont agitées et chauffées par des serpentins à vapeur. Lorsque la température descend en dessous d'un point donné, les agitateurs sont activés et la vapeur est envoyée aux serpentins, maintenant ainsi la solution à la température souhaitée.
Un convoyeur à vis flexible transporte le nitrate de sodium granulaire de la station de vidange de Big Bags vers les cuves chauffées, où il se dissout dans le nitrate d'ammonium. La solution préparée est ensuite transférée à une table de mélange, où elle est combinée à un mélange de quatre combustibles, dont l'un sert d'émulsifiant. L'émulsification est pompée vers une cuve de rétention, puis vers une autre zone de l'usine, où des granulés solides de nitrate d'ammonium sont ajoutés à l'aide d'une vis sans fin. Le produit final est ensuite déchargé dans un camion pour être livré.
Déchargement de nitrate de sodium à partir de Big Bags
Chaque lot nécessite 4 535 kg de nitrate de sodium livrés dans cinq Big Bags de 907 kg, qui sont vidés à l'aide d'une station de vidange de Big Bags fabriquée par Flexicon. La station de vidange de Big Bags est équipée d'un cadre de levage de sacs amovible qui se connecte aux sangles du Big Bag, et est soulevé par un chariot élévateur jusqu'au berceau situé au sommet du cadre de la station. Au fur et à mesure que le sac se vide et s'allonge, les dispositifs d'extension de sac POP-TOP™ montés sur le dessus du cadre étirent le sac pour lui donner une forme de cône, favorisant ainsi le déchargement complet du matériau dans la trémie.
L'interface entre la manchette du sac et la trémie de 0,085 m3 est constituée d'un collier de serrage SPOUT-LOCK™ placé sur un tube télescopique TELE-TUBE™. Le collier de serrage crée une connexion étanche à la poussière à haute intégrité entre le côté propre de la manchette de sortie du sac et le côté propre de l'équipement. Le tube télescopique est soulevé grâce à une commande pneumatique, permettant au collier de serrage de se connecter à la manchette du sac, puis abaissé, en appliquant une tension continue vers le bas pour allonger le sac et maintenir la manchette tendue, empêchant le matériau dans la manchette de créer des renflements (poches mortes) ou de s'accumuler à l'intérieur (créant des restrictions d'écoulement).
Une vanne de réglage de débit POWER-CINCHER™ à commande pneumatique régule le flux de matériau s'écoulant du sac. L'appareil contient une série de tiges courbes et articulées en acier inoxydable qui serrent la manchette du sac de façon concentrique pour éliminer les fuites, et qui s'ouvrent à un diamètre plus large que celui de la manchette pour permettre un déchargement sans restriction.
Convoyage des matériaux vers les mélangeurs
Le nitrate de sodium granulaire est transporté de la trémie jusqu'aux cuves de mélange par trois convoyeurs à vis flexibles également fabriqués par Flexicon. Chaque convoyeur de 6 m est constitué d'une spirale en acier inoxydable robuste, qui tourne dans un tube en polymère flexible de 11 cm de diamètre extérieur grâce à un moteur électrique de 5,6 kW avec une boîte à engrenages située à l'extrémité de déchargement de chaque unité.
L'extrémité d'alimentation de chaque convoyeur est équipée d'une auge en forme de U qui sert d'adaptateur de chargement. Une portion de la vis rotative passe dans l'auge et la vis propulse le matériau à travers le tube. Le tube extérieur du premier convoyeur est fixé à la trémie à l'aide d'un raccord mécanique, et l'extrémité d'alimentation de la vis se prolonge dans la trémie.
Le premier convoyeur transporte le matériau à partir de la trémie à une inclinaison de 45 degrés et le décharge dans l'adaptateur de chargement d'un deuxième convoyeur identique qui, lui, est connecté en série ; ensemble, ils transportent le matériau sur une distance horizontale d'environ 8,5 m. Le deuxième convoyeur se vide dans une vanne d'aiguillage (actionnée manuellement par un sélecteur bidirectionnel sur le panneau de commande), qui verse le produit soit directement dans un mélangeur, soit dans l'adaptateur de prélèvement d'un troisième convoyeur pour le transporter vers un autre mélangeur situé à une distance de 5 m.
Des capteurs de proximité capacitifs surveillent les niveaux de matériau dans la trémie et dans l'ensemble du système, signalant à un contrôleur de démarrer et d'arrêter les convoyeurs. Les capteurs de niveau dans les zones de transition (où le premier convoyeur se décharge dans le second et où le second se décharge dans la vanne d'aiguillage) déclenchent l'arrêt d'un convoyeur si la transition suivante est pleine; lorsque le niveau baisse, le contrôleur redémarre le convoyeur.
Le nouveau procédé a permis d'éliminer les déversements au niveau des boîtes à boue, améliorant ainsi la propreté de l'usine tout en réduisant le gaspillage de matériaux.
«Il est beaucoup plus facile de balayer une petite quantité de matériau granulaire que de nettoyer les déversements de liquide, qui devaient autrefois être acheminés dans une fosse d'aspiration et traités avec les eaux uses», souligne M. King, «à présent si des granulés tombent au sol, nous les récupérons pour les remettre dans le mélangeur, de sorte qu'aucun matériau n'est perdu».
Les coûts ont été réduits en éliminant le besoin d'une personne pour surveiller le niveau de la boîte à boue. Un seul opérateur s'occupe désormais de toutes les tâches de déchargement des sacs.
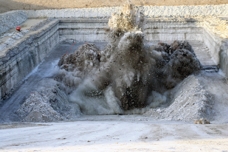
En savoir plusFournie par Dykon Blasting Corp. Minnesota Explosives fabrique des explosifs en vrac pour le dynamitage de taconite.
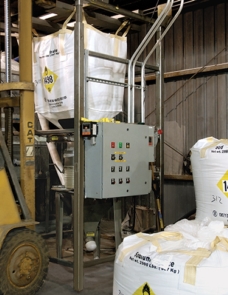
En savoir plusUn cadre de levage de sacs amovible se connecte aux sangles du Big Bag, et est soulevé par un chariot élévateur jusqu'au berceau situé au sommet du cadre de la station.
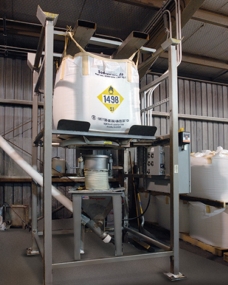
En savoir plusLa station de vidange de Big Bag utilise des dispositifs d'extension de sac POP-TOP™ qui étirent le sac pour lui donner une forme de cône lorsqu'il se vide, favorisant ainsi le déchargement complet des granulés de nitrate de sodium.
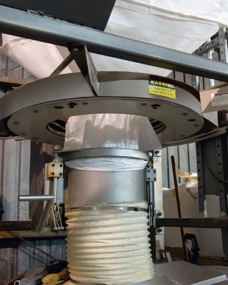
En savoir plusUn collier de serrage SPOUT-LOCK™ créé un joint à haute intégrité entre le côté propre du sac et le côté propre de l'équipement, tandis qu'un tube télescopique TELE-TUBE™ maintient une tension sur la manchette du sac pour allonger le sac au fur et à mesure qu'il se vide, favorisant le déchargement complet.
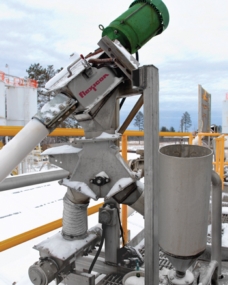
En savoir plusUne vanne d'aiguillage dirige le matériau du deuxième convoyeur directement dans une cuve de mélange ou dans un troisième convoyeur qui se décharge dans un autre réservoir.
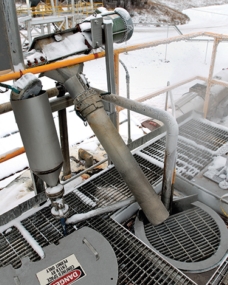
En savoir plusLe matériau passe dans la vanne d'aiguillage puis dans un tube d'alimentation et est versé dans la première cuve de mélange.
T-0933