Un producteur de lubrifiant triple sa capacité avec un système de convoyage/déchargement en vrac
MANCHESTER, ROYAUME-UNI — M & I Materials Ltd. a enregistré des augmentations allant jusqu'à 194 % du volume produit d'un lubrifiant qu'elle fabrique pour les transformateurs électriques, principalement grâce à l'ajout d'une station de vidange de Big Bags et d'un convoyeur à vis flexible de Flexicon.
Avant l'installation, le débit moyen était de 16 à 20 tonnes par semaine de lubrifiant MIDEL 7131. La production actuelle est de 47 tonnes par semaine. Le gain de productivité et les avantages qui en découlent, à savoir l'amélioration de la sécurité des travailleurs et de la qualité des produits et une rentabilité accrue, sont le résultat de deux nouvelles installations et d'un déménagement de l'usine. M & I a doublé la production de lubrifiant MIDEL avec la première installation de l'équipement Flexicon dans son ancienne usine d'Old Trafford, au Royaume-Uni, et a triplé la production après le déménagement à Manchester et la construction d'un réacteur de traitement plus grand.
M & I Materials fabrique des huiles industrielles, des graisses et des produits métallurgiques en poudre. MIDEL 7131, un fluide à base d'ester synthétique sans halogène, est l'un de ses produits les plus connus. La demande de lubrifiant augmente en raison de son efficacité en tant qu'isolant, de sa biodégradabilité et de sa composition non toxique, qui conviennent à son utilisation dans des applications respectueuses de l'environnement et facilitent l'élimination.
La manipulation manuelle de la matière affectait le taux de production
La fabrication du lubrifiant MIDEL consiste à mélanger de la matière première — ester de monopentaérythritol, ou «penta» — avec divers acides sous pression et chauffés dans un réacteur. Les matières premières était expédiées à M & I dans des sacs de 25 kg qui étaient stockés sur une mezzanine, sélectionnés manuellement et déplacés de 5 mètres à l'un des deux réacteurs de traitement. Là, les sacs étaient ouverts par les travailleurs et acheminés par gravité par une trappe dans un réservoir de prémélange qui était déjà chargé d'acides. Chaque lot nécessitait 225 kg de penta. Après le chargement d'un lot dans l'un des deux réacteurs d'une capacité de 1 tonne, le traitement durait neuf heures.
La procédure présentait des inconvénients. L'utilisation de sacs de 25 kg empêchait M & I de réaliser des économies d'échelle en achetant du penta en vrac. Une partie du produit a été perdue lors de l'ouverture des sacs et du chargement de la matière première. La contamination par l'humidité provoquait la solidification d'une partie du penta qui formait des en morceaux, ce qui affectait le déchargement et pouvait endommager l'équipement de traitement. La manutention manuelle présentait un risque de blessure pour les travailleur; et il y avait des dangers d'inhalation, même si le personnel de l'usine avait des équipements de sécurité et qu'un ventilateur aspirant avait été installé sur le réacteur pour aspirer la poussière. De plus, les sacs de penta vides engendraient des coûts d'élimination des déchets. Au fur et à mesure que la demande pour le produit augmentait, le besoin d'un moyen d'accroître la productivité et la sécurité au travail augmentait.
Flexicon a travaillé en collaboration avec les ingénieurs de M & I pour concevoir, installer et mettre en ligne un système de déchargement et de convoyage de Big Bags qui a doublé la production de l'usine d'Old Trafford passant à 32 tonnes par semaine. Le système a été conçu pour manipuler des chargements d'une tonne de penta expédiés dans des Big Bag (aussi connus sous le nom de flexible intermediate bulk containers ou GRVS). M & I a donc été en mesure de remplacer les sacs de 25 kg par des Big Bags des achats plus économiques.
Le système se compose d'un cadre de Big Bag de 4 mètres de haut équipé d'un palan motorisé et d'un chariot, monté sur des pesons pour une mesure précise de la perte de poids ; d'une trémie de 200 litres équipée d'agitateurs mécaniques pour assurer un flux régulier du matériau dans la gorge du convoyeur; d'un convoyeur à vis flexible de 4 mètres de long avec un tube en polymère haute performance, alimenté par un entraînement par engrenage de 2,2 kW; un adaptateur de déchargement-transition qui dirige le matériau vers un réservoir de prémélange; et un panneau de contrôle.
Le chargement commence par un chariot élévateur qui transporte un conteneur de penta en vrac jusqu'à l'aire d'entreposage temporaire. Le Big Bag est fixé aux quatre coins d'un berceau de levage par palan et positionné dans le cadre de Big Bag au-dessus de la trémie par l'intermédiaire du palan motorisé et du chariot intégrés. Par une porte dans la goulotte entre le cadre et la trémie, un travailleur tire la manchette de sortie du matériau au niveau de la face inférieure du Big Bag et la fait passer dans une vanne Iris, qui se ferme ensuite pour empêcher les déversement accidentels alors que les liens de déchargement du conteneur sont ouverts. La vanne Iris est généralement ouverte complètement pour permettre la vidange complète du penta dans la trémie. Cependant, la vanne peut être ouverte à des degrés divers pour réguler le flux du matériau. Une fois dans la trémie, le penta est acheminé par gravité jusqu'au convoyeur, qui le transporte à un angle de 45 degrés vers le réservoir de prémélange. Les pesons du système permettent de peser avec précision le penta à mesure que le produit est déchargé dans le réservoir de pré-mélange.
Le système de manutention de matière vrac a permis d'augmenter la capacité et de réduire les coûts
Grâce à la plus grande capacité de manutention de matière vrac de l'équipement Flexicon, jusqu'à quatre lots de 225 kg pouvaient être mélangés avec des acides dans le réservoir de prémélange, ce qui a permis d'augmenter la production. Les ingénieurs de M & I ont également installé un réservoir de décapage à l'acide à côté du réservoir de prémélange. Le réservoir de décapage à l'acide a permis d'éliminer les acides excédentaires du lot par estérification. Cela se faisait auparavant dans les réacteurs. Le réservoir de prémélange et le réservoir de décapage à l'acide ont été conçus avec un système d'échange de chaleur partagé, ce qui a réduit le temps de traitement de 9 heures à 5 heures, augmentant ainsi la quantité de matière pouvant être mélangée. Après estérification, le mélange a été transféré dans l'un des deux réacteurs.
Lorsque M & I a déménagé son usine à Manchester, la système de convoyage et de vidange de Big Bags Flexicon a dû être légèrement modifié parce que les ingénieurs de l'entreprise ont opté pour un seul réacteur de 5 tonnes à la place des réacteurs d'une tonne à Old Trafford. Cela a éliminé le besoin d'un réservoir de prémélange de lots, puisqu'il pouvait contenir des lots de 900 kg. Le nouveau réacteur peut traiter 4,5 tonnes toutes les 12 heures, soit 47 tonnes par semaine de travail. Pour répondre aux besoins en matériaux du nouveau réacteur, Flexicon n'avait qu'à augmenter la hauteur du cadre de la station de vidange de Big Bags de 4 m à 6 m et à prolonger le convoyeur de 2 m.
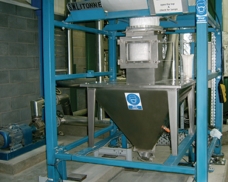
En savoir plusLa goulotte entre le conteneur de vrac et la trémie de 200 L est équipée d'une porte d'accès pour que le travailleur puisse tirer la manchette de sortie du matériau située sur la face inférieure du Big Bag sur la valve Iris avant le déchargement.
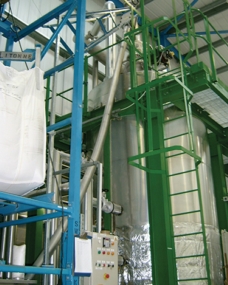
En savoir plusUn convoyeur à vis flexible de 6 m de long dans un tube en polyéthylène transporte le penta de la trémie à l'adaptateur de transition/déchargement, où il est déchargé par gravité dans le réacteur de 5 tonnes de l'usine M & I de Manchester, au Royaume-Uni.
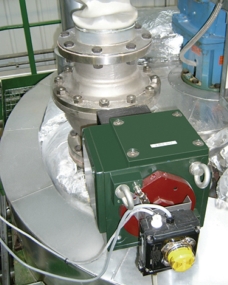
En savoir plusGros plan sur l'adaptateur de déchargement/transition qui verse le penta directement dans le réacteur à partir du convoyeur à vis flexible.
T-0564