Deux convoyeurs de vrac valent mieux qu'un seul
Les caractéristiques chimiques isotopiques nécessitent l'intégration de convoyeurs mécaniques et pneumatiques pour la précision du dosage.
QUAPAW, OK — Pour fabriquer des produits chimiques et isotopiques à haut degré de pureté, EaglePicher Technologies a mis au point un nouveau procédé dans lequel cinq produits en vrac sont transférés, pesés avec une grande précision et transportés vers un système de mélange.
Les ingénieurs d'EaglePicher connaissaient la recette du lot et le résultat final, mais n'étaient pas intéressés par une technologie de convoyage ou une conception d'équipement en particulier. Après des discussions avec plusieurs fournisseurs d'équipement et un processus d'appel d'offres, EaglePicher a finalement choisi une conception unique de Flexicon qui combinait des convoyeurs à vis flexibles et un centre pesé par lot pour répondre aux exigences de mesure exactes au début du processus, avec un convoyage pneumatique par aspiration en aval pour transférer 100 % des ingrédients pesés vers le processus de mélange final.
Cinq ingrédients, deux routes
Le procédé breveté d'EaglePicher consiste à mélanger cinq produits séchés, quatre fournis dans des Big Bags et un dans des sacs de 23 kg avec de l'eau. Les ingrédients sont des poudres fines, à écoulement relativement facile, sèches et générant facilement de la poussière. L'humidité dans le système doit être contrôlée pour éviter l'absorption de l'humidité ambiante par le matériau sec.
Deux des ingrédients vont directement dans un mélangeur humide, et les trois autres ingrédients sont d'abord acheminés vers un mélangeur à sec pour être mélangés, puis vers le mélangeur humide. Le poids des ingrédients pour la recette du lot varie d'un minimum de moins de 9 kg à un maximum de près de 181 kg dans chaque lot, et le processus exige une précision de +/- 1,00 % du poids cible de tous les ingrédients, ainsi que de l'eau.
La conception combine le convoyage mécanique et pneumatique pour plus de precision
Le processus exigeait un équipement de déchargement des système de dosage par pesée avec convoyage des poudres. Flexicon a proposé un centre de dosage par lot par gain de poids utilisant des convoyeurs à vis flexibles pour déplacer les ingrédients des trémies de déchargement des sacs, et des lignes de convoyage pneumatique pour déplacer les ingrédients pesés vers la destination désirée. Voir la figure 1 pour un schéma d'ensemble du système.
Les Big Bags sont déchargés à l'aide de déchargeurs en I en porte-à-faux équipées de palans électriques et de chariots élévateurs, ce qui élimine le besoin d'un chariot élévateur. Les stations de vidange de Big Bags (Figure 2) font partie d'un système hermétique qui retient la poussière et favorise l'écoulement et l'évacuation totale du matériau.
Le cinquième ingrédient mineur est déchargé manuellement dans une trémie vide-sacs avec collecteur de poussière. L'opérateur vide plusieurs sacs à la fois dans la trémie, la remplissant avec suffisamment de matériau pour une semaine.
Les ingrédients sont transférés via des convoyeurs à vis flexibles (Figure 3) vers le système de pesage par lots. Chacun des cinq convoyeurs à vis est conçu spécifiquement pour la poudre déplacée, avec des tailles, des matériaux de construction et des conceptions de vis différentes en fonction de la masse volumique apparente et des propriétés d'écoulement de chaque matériau. Les convoyeurs à vis flexibles sont un choix idéal pour ce type d'application, chaque convoyeur est conçu pour un matériau particulier offrent une grande précision et fiabilité et un entretien réduit.
Le système de dosage par gain de poids (Figure 4) mesure les ingrédients en séquence au fur et à mesure qu'ils s'écoulent dans la trémie de pesée centrale. Les pesons transmettent des informations de gain de poids à un contrôleur qui démarre et arrête les convoyeurs, ralentissant la vitesse d'alimentation à un goutte-à-goutte lorsque le poids s'approche du poids cible afin de répondre aux exigences de précision extrême. Un vanne guillotine située au bas de la trémie de pesée décharge l'ingrédient.
Puisqu'il y a deux destinations différentes pour les flux d'alimentation de matériau pesé, une vanne d'aiguillage en Y spécialement conçue envoie chaque ingrédient à l'endroit désiré: soit le mélangeur à sec ou le mélangeur humide. Les deux premiers ingrédients contournent le mélangeur à sec situé juste en dessous du système de dosage par poids et s'écoulent dans une écluse rotative puis dans le système de convoyage pneumatique par aspiration qui les amène au mélangeur humide. Là, ils sont pré-mélangés avec de l'eau et on leur donne le temps de se mélanger. Les trois autres ingrédients passent dans la vanne d'aiguillage puis s'écoulent directement dans le mélangeur à sec, où ils sont mélangés pendant 30 minutes. Ce mélange est ensuite déchargé par le fond du mélangeur à sec dans la même écluse rotative puis dans le même système de convoyage pneumatique pour être transféré dans le mélangeur humide.
Le système de convoyage pneumatique a été choisi pour sa capacité à traiter les divers types de poudres ayant des caractéristiques différentes et parce que le système se videra automatiquement du matériau qu'il transporte. Puisque le système de convoyage pneumatique vide complètement le conteneur en cours de déchargement, ainsi que la ligne de convoyage elle-même, la contamination croisée est réduite au minimum dans ce système à ingrédients multiples. Le transfert complet du matériau permet également de s'assurer que les lots d'ingrédients individuels et groupés atteignent correctement leur destination en fonction de leur poids.
Chacun des ingrédients secs sortant du convoyeur pneumatique est recueilli dans un filtre de réception équipé d'un filtre à jet d'impulsion inversé pour déloger la poussière accumulée sur les surfaces du filtre, assurant ainsi la séparation complète du matériau du flux d'aspiration (Figure 5). La trémie de réception du filtre utilise un module de pesage avec pesons pour confirmer le transfert complet du lot. Une autre écluse rotative prélève la poudre directement dans le mélangeur humide situé en dessous. Une pompe à vide volumétrique de 15 kW située en aval du filtre de réception fournit un débit d'air suffisant pour transférer tous les matériaux.
Les ingénieurs Flexicon étaient sur place pendant le démarrage pour former les opérateurs. Selon Loren Harding, directeur des opérations d'EaglePicher, le système de convoyage intégré répond à toutes les exigences du processus et prévient la contamination du produit et de l'environnement de l'usine.
EaglePicher a porté son choix final sur Flexicon pour plusieurs raisons. M. Harding explique: «Flexicon avait l'expérience nécessaire en marière de pesage et du dosage par lot pour fournir un système clé en main intégré unique, y compris des commandes reliées à un contrôle logique programmable, avec une précision garantie. De plus, la station de vidange de Big Bags de Flexicon avec interface sac-manchette brevetée, était la meilleure option que nous ayons rencontrée pour garantir un système hermétique pendant toute la durée le déchargement. Enfin, et c'est peut-être le plus important, Flexicon a été la seule entreprise à proposer un système pneumatique par aspiration combiné à un concoyage mécanique, la solution la plus avantageuse pour nos besoins».
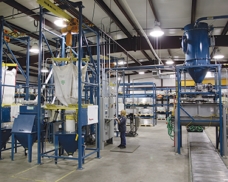
En savoir plusFigure 1: Une combinaison de vis flexible et de convoyage pneumatique répond aux exigences du processus, avec cinq convoyeurs à vis flexible transportant les ingrédients vers un système de dosage par poids, et le système de convoyage pneumatique par aspiration transportant les ingrédients secs pesés et mélangés vers le mélange humide.
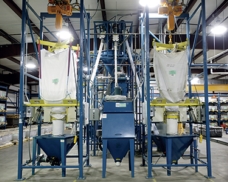
En savoir plusFigure 2: Les stations de vidange de Big Bags utilisent une interface exclusive sac-manchette qui crée une connexion scellée à haute intégrité pour retenir la poussière et prévenir la contamination du produit et de l'environnement de l'usine. Une trémie vide-sacs manuelle avec collecte de poussière (au centre) protège les travailleurs et prévient la contamination de l'usine.
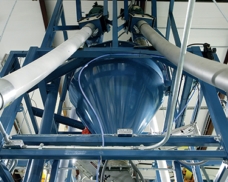
En savoir plusFigure 3: Les convoyeurs à vis flexible ralentissent la vitesse d'alimentation à un goutte-à-goutte pour la précision de la mesure des ingrédients (variation par rapport aux objectifs de la recette de 1 %), et isolent également les poudres de l'humidité dans l'air de l'usine.
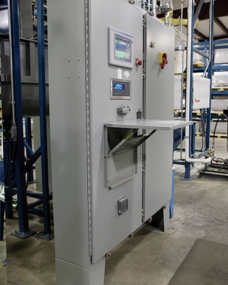
En savoir plusFigure 4: Un système de contrôle automatisé gère l'ensemble du processus conformément aux recettes de lots préprogrammées.
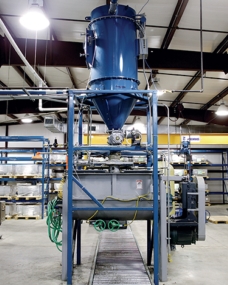
En savoir plusFigure 5: Un filtre de réception avec nettoyage par jets d'air inversés sépare efficacement et en continu la poudre du système pneumatique par aspiration, en faisant tomber la poudre dans le mélangeur humide.
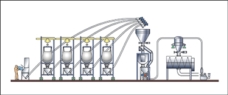
En savoir plus(G-D) Cinq convoyeurs à vis flexibles transportent les poudres d'une trémie vide-sacs et de quatre stations de vidange de Big Bags vers une trémie par gain de poids montée sur des pesons. Trois des ingrédients sont pesés par lots, déchargés par gravité de la trémie dans un mélangeur à sec, puis une quantité mesurée est versée dans une ligne de convoyage pneumatique qui se termine par un filtre de réception qui lui-même se décharge dans un mélangeur humide. Les deux autres ingrédients sont pesés de la même manière, mais ils contournent l'étape de mélange à sec et sont plutôt versés directement dans la ligne de convoyage pneumatique qui se termine par une filtre de réception et se décharge dans le mélangeur humide, où les cinq ingrédients sont combinés.
T-0477