Le système de manutention en vrac permet à un boulanger-pâtissier de réaliser d'importants gains de productivité et d'économie
EDINBURGH, Royaume-Uni — Lorsque Simmers of Edinburgh Ltd, un fabricant de biscuits spécialisés, a entrepris de moderniser son usine de transformation, l'entreprise a cherché des moyens d'améliorer la manutention des sacs de farine d'avoine en vrac utilisés dans la préparation de plusieurs marques de biscuits. L'objectif était d'automatiser autant que possible le processus et de convertir les sacs de 35 kg qui étaient manipulés manuellement dans toute l'usine en grosses quantités d'une tonne.
Simmers traite trois grades de farine avoine — «ête d'épingle», grains moyens et grains fins — dans son usine d'Édimbourg de 2 232 m2. Chaque grade était livré dans des sacs de 35 kg. Les travailleurs transféraient les sacs des palettes entrantes sur des palettes en plastique, chargeant chacun jusqu'à 20 sacs. Les sacs palettisés étaient ensuite déplacés d'environ 30 m à travers l'entrepôt jusqu'à une station de traitement. Huit sacs de différentes combinaisons de grains (formant un lot) étaient ensuite ouverts grâce à des languettes d'arrachage et vidés manuellement dans un récipient de 800 mm de haut pour être mélangés à d'autres ingrédients.
La manutention manuelle des Big Bags était inefficace et coûteuse
L'opération présentait de nombreux inconvénients. Notamment l'émanation de poussières, qui soulèvent des problèmes de santé des travailleurs, des pertes de produits dues aux déversements et aux résidus de sacs, et des problèmes de contrôle de la qualité découlant de la vidange manuelle des sacs dans le mélangeur. Il y avait aussi les frais d'achat de farine d'avoine en sacs de 35 kg plutôt qu'en sacs de plus grande taille, et les coûts d'élimination de plusieurs dizaines de milliers de sacs vides chaque année. En outre, une loi limitant le poids des sacs manipulés par les travailleurs à 25 kg allait bientôt devenir obligatoire, ce qui aurait obligé Simmers à commander de la farine d'avoine en quantités encore plus petites et plus coûteuses.
La solution développée par Flexicon était simple et efficace. L'entreprise a conçu et installé un système de déchargement de Big Bags qui traite des sacs d'une tonne de farine d'avoine à grain moyen. Ce grade a été choisi parce qu'il s'agit du type le plus couramment utilisé dans le processus de mélange de Simmers. Le système de déchargement des Big Bags comprend six éléments: un cadre de Big Bags monté sur quatre pesons; une poutre en I en porte-à-faux avec palan électrique et chariot; une trémie de 200 L; un convoyeur à vis flexible de 7 m de long, alimenté par un moteur de 1,5 kW; et un panneau de contrôle par perte de poids.
Toutes les pièces en contact avec les aliments sont fabriquées en acier inoxydable de haute qualité ou, dans le cas du tube de convoyage, en polyéthylène de poids moléculaire très élevé. Ces deux matériaux sont conformes aux réglementations locales en matière de sécurité alimentaire. En raison du manque d'espace, le système de déchargement de Big Bags a été installé dans l'entrepôt, séparé de l'usine par un mur.
Le convoyage et le mélange de farine d'avoine est plus efficace et plus précis avec le système de déchargement de Big Bags de Flexicon. Un sac d'une tonne est transporté jusqu'à la station de déchargement sur un transpalette. Avec le palan et le chariot, l'opérateur positionne le Big Bag au-dessus de la trémie. Une vanne Iris restreint le débit du produit pendant que l'opérateur ouvre la manchette de vidange du Big Bag. Une fois le sac détaché, la valve Iris est ouverte et le farine d'avoine s'écoule dans la trémie. Un capteur de niveau bas dans la trémie avertit automatiquement l'opérateur lorsqu'il faut charger plus de farine d'avoine.
À partir de la trémie, le matériau est acheminé par gravité dans la gorge du convoyeur à vis flexible. La vis auto-centrante transporte le matériau à un angle de 15 degrés vers le haut à travers le mur séparant l'entrepôt de l'usine. L'information de perte de poids fournie par le panneau de commande Flexicon automatise le fonctionnement du convoyeur à vis flexible, délivrant la plus grande partie du lot requis à grande vitesse et ralentissant la vitesse du convoyeur jusqu'à atteindre un goutte-à-goutte lorsque le poids du lot est presque atteint pour obtenir une grande précision. À l'extrémité du convoyeur, du côté opposé de la paroi, la farine d'avoine est versée par gravité par l'intermédiaire d'un adaptateur de transition vers le récipient de mélange dans la zone de traitement. Flexicon a installé des commandes de démarrage/arrêt sur la station de déchargement et à l'extrémité du convoyeur dans la zone de traitement pour une sécurité maximale.
Le système de déchargement de matière vrac améliore la manutention des produits et le contrôle de la qualité
Le système de déchargement de Big Bags de Flexicon a été un succès sans précédent pour Simmers. Les émissions de poussière ont été considérablement réduites; les opérations manuelles ont été réduites au minimum; le contrôle de la qualité a été amélioré grâce à la fonction de mesure automatisée du système; des économies d'échelle plus importantes ont été réalisées en achetant de la farine d'avoine en grains moyens dans des sacs d'une tonne; et les coûts d'élimination des sacs ont été considérablement réduits.
Le système a si bien fonctionné que Simmers a demandé à Flexicon de concevoir et installer une deuxième unité, pour la farine d'avoine «tête d'épingle». L'adoption de la législation qui a réduit le poids des sacs que les travailleurs peuvent porter à 25 kg, ce qui aurait nécessité la commande et l'élimination d'un plus grand nombre de sacs plus petits a motivé ce choix.
Le deuxième système de déchargement de Big Bags, installé à côté du premier, vide les sacs dans une trémie plus petite de 80 L. Un convoyeur à vis flexible de 2,9 m de long part latéralement de la station de déchargement pour éviter un silo obstruant le passage dans la zone de l'usine, puis transfère le matériau à angle droit vers un deuxième convoyeur à vis flexible de 7 m de long, qui traverse le mur jusqu'à la zone de l'usine où la farine d'avoine «tête d'épingle» se vide par gravité dans un adaptateur de transition puis dans le récipient de mélange. Comme pour le système d'origine, des commandes de démarrage/arrêt ont été installées sur les stations de déchargement et de mélange.
Le système de déchargement de Big Bags que Flexicon a conçu pour la farine d'avoine «tête d'épingle» a permis d'obtenir tous les avantages du premier système, y compris des avantages notables en matière de propreté, d'efficacité de la production, de contrôle de la qualité et d'économies d'échelle. Ensemble, ces systèmes permettent à Simmers d'éliminer le coût d'élimination de quelque 89 000 sacs en papier par année.
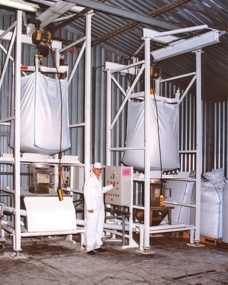
En savoir plusFlexicon a conçu et installé deux systèmes de déchargement de vrac chez le fabricant de biscuits Simmers of Edimbourg Ltd. L'un est pour la farine d'avoir à grain moyen (à gauche), l'autre pour la farine d'avoine à grain fin.
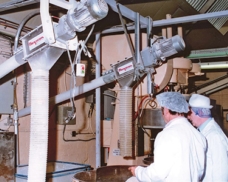
En savoir plusFlexicon a ajouté un convoyeur à vis flexible de 7 m de long pour transférer la farine d'avoine de la station de déchargement à la zone de mélange.
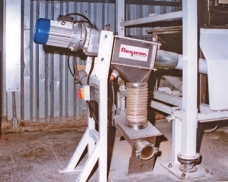
En savoir plusLes convoyeurs à vis flexibles des deux systèmes de manutention de déchargement de vrac se déplacent parallèlement dans la station de mélange.
R-0167