Le système de transfert en vrac triple la quantité d’additif alimentaire sec produite
HALESOWEN, ROYAUME-UNI — Un système de transfert de produit automatisé composé d'une station de vidange de Big Bags et de convoyeurs à vis flexibles a permis de tripler la production de l'ingrédient sec de Drywite Ltd. pour traiter les pommes de terre coupées pour les poisson et frites. Le système permet à l'entreprise britannique de satisfaire la demande mondiale croissante pour son produit «Drywite», qui conserve les pommes de terre coupées avant la friture pour une meilleure tenue et un aspect moins gras.
L'ancien système limitait la capacité de production
Avant l’installation du nouveau système, trois opérateurs vidaient continuellement des sacs de 23 kg du matériaux en vrac et des additifs nécessaires à la préparation de Drywite dans une trémie montée au sol à partir de laquelle un convoyeur à disques transportait le produit vers un silo d’une capacité de 998 kg. Le mélange était acheminé par gravité jusqu’à la ligne d’emballage du remplisseur à vis sans fin. Le changement de formulation présentait des difficultés parce que le matériau en vrac devait être entièrement consommé avant le changement de produit. La production était limitée à 1.8 – 2.7 tonnes par jour.
Avec le nouveau système, conçu par les propres ingénieurs de Drywite et Flexicon, les convoyeurs à vis flexibles simplifient le processus de dosage et transportent les produits en vrac en provenance de et vers deux silos qui alimentent les machines d'emballage à vis sans fin. Une station de vidange de Big Bags en trois parties à cadre détachable déplace trois fois plus de matériaux qu'auparavant tout en tenant compte le manque de hauteur sous plafond.
Le système se compose d'un cadre de station de vidange de Big Bags en trois parties, d'une trémie de réception, d'un convoyeur à vis incliné, d'un convoyeur à vis horizontal, de deux silos et d'une trémie de basculement de sac avec un doseur volumétrique pour le dosage de l'additif spécial. Le système est automatisé par deux panneaux de contrôle, l'un situé dans la ligne de production et l'autre dans la ligne d'emballage, afin de permettre le fonctionnement des deux zones de l'usine. De plus, Flexicon a installé une unité de dépoussiérage.
Cadre de station de vidange de Big Bags en trois parties s'adapte au manque de hauteur
Pour un fonctionnement sous faible hauteur libre, le cadre de station de vidange de Big Bags se divise en trois parties: le cadre cruciforme, le cadre intermédiaire et le cadre de base. Un chariot élévateur charge le cadre cruciforme avec un Big Bag suspendu sur le cadre intermédiaire au niveau du sol, à distance du cadre de base. Une fois le Big Bag en place, le cadre intermédiaire est ensuite manœuvré entre deux éléments de plafond et, avec un dégagement minimal par rapport au plafond, est soulevé sur le cadre de base.
Lorsque le Big Bag est en place au-dessus de la trémie de réception, la manchette du sac est passée dans une vanne Iris et dans la bouche d'alimentation de la trémie dont la porte à dégagement rapide donne accès pour ouvrir ou fermer la manchette du sac sans débordement.
La membrane flexible de la vanne Iris, qui se ferme autour da la manchette à l'aide d'un levier manuel, contrôle la vitesse à laquelle le produit en vrac s'écoule, empêchant les déversements incontrôlés de produit dans la trémie de réception et l'émanation de poussière dans l'environnement.
Lorsque le Big Bag est déchargé, les plaques FLOW-FLEXER™ soulèvent les côtés inférieurs opposés du Big Bag à intervalles réguliers afin de favoriser l'écoulement des matériaux à écoulement facile, difficile ou compactés dans la manchette du sac. Au fur et à mesure que le sac se vide, la pressions des plaques augmente, soulevant le fond du sac pour lui donner une forme de «V», éliminant ainsi les zones mortes et favorisant le déchargement complet. Un dispositive «Flexi-Finger» monté sur une paroi intérieure de la trémie assure un flux ininterrompu de matériau dans l'entrée du convoyeur à vis flexible.
A côté de la trémie de réception se trouve la trémie de basculement du sac, qui mesure la quantité d’additif versée au moyen d’un doseur volumétrique, dans la gorge du convoyeur à vis flexible alimentant les deux silos d’une capacité de 1.8 tonnes. Le mélange final est mélangé au fur et à mesure qu’il passe dans le convoyeur à vis flexible de 4.25 m de long à 45° vers les silos, qui alimentent les vis sans fin des lignes d’emballage via deux convoyeurs à vis flexibles passant à travers une paroi.
Les capteurs de niveau à la base des trémies sont reliés à un système de contrôle qui arrête le fonctionnement dès réception d'un signal de niveau bas et alerte l'opérateur, assurant un dosage précis.
Choix plus large de formulations
Les deux silos contiennent collectivement 3.6 tonnes d’une formulation, ou 1.8 tonnes chacune de formulations séparées. Une tonne supplémentaire de matière est maintenue en ligne dans le Big Bag. Lorsque l'additif est complètement déchargé, l'opérateur peut modifier la formulation. Après l'ouverture d'une vanne et l'inversion du sens de rotation de la vis du convoyeur pour le nettoyage sur place, le nouvel additif peut être chargé dans le doseur volumétrique et le processus peut redémarrer. Depuis le panneau de commande, l'opérateur actionne une vanne guillotine au sommet du premier silo pour faire passer le flux de produit dans un convoyeur à vis horizontal vers le second silo. Ainsi, la ligne de conditionnement peut recevoir deux formulations du traitement Drywite.
Les temps d'arrêt pour le nettoyage et les changements de produits sont considérablement réduits. Le système automatisé de transfert de produits permet également d'augmenter la capacité de production sans investissement supplémentaire. Comme l'opérateur n'est nécessaire que lorsque le capteur signale la présence de matières supplémentaires, les deux tiers du temps auparavant consacré au déversement manuel sont maintenant affectés à des tâches ailleurs dans l'usine.
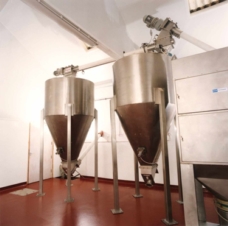
En savoir plusLe convoyeur transversal horizontal permet le remplissage sélectif de silos qui se déversent dans des convoyeurs et achemine le produit au travers de l'usine pour alimenter une ligne d'emballage.
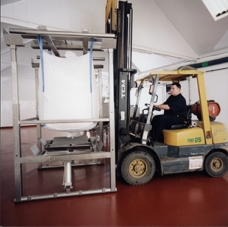
En savoir plusLe chariot élévateur charge le sac dans un châssis intermédiaire éloigné du châssis de base.
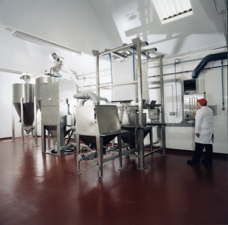
En savoir plusLe chariot élévateur positionne le cadre intermédiaire contenant le sac entre les traverses pour le positionnement sur la trémie d'alimentation.
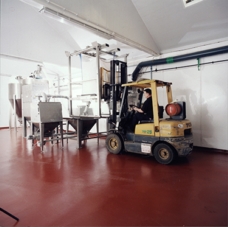
En savoir plusLe système complet avec l'opérateur programmant les paramètres de fonctionnement nécessaires.
P-0208