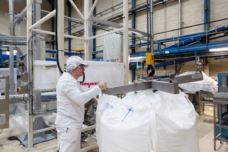
En savoir plusL'opérateur fixe le big bag au cadre de levage à l'aide des supports de sangle de sac Z-Clip™ avant de hisser le sac dans le châssis du déchargeur.
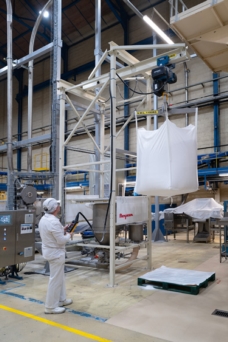
En savoir plusÀ l'aide d'une télécommande, l'opérateur hisse un big bag de sucre extra-fin le long de la poutre en porte-à-faux jusqu'au châssis du déchargeur.
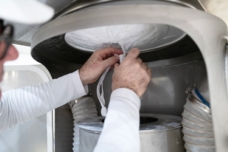
En savoir plus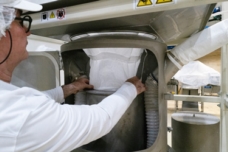
En savoir plusL'opérateur détache la goulotte du sac, ce qui permet au sucre de s'écouler dans la trémie de réception et, par le biais d'une vanne rotative, dans la ligne de transport pneumatique Pneumati-Con®. À gauche et à droite, des raccords flexibles évacuent la poussière vers des chaussettes filtrantes.
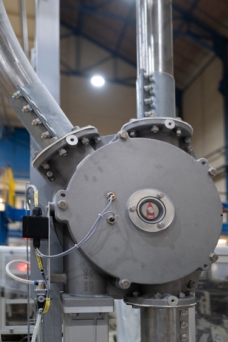
En savoir plusUn déviateur wye dirige le sucre soit sur 20 m vers le procédé humide pour la production de morceaux de sucre, soit sur 8,5 m vers la ligne d'emballage.
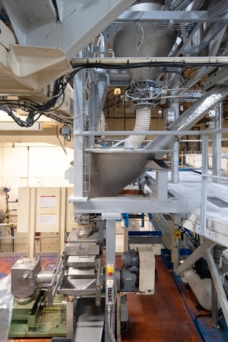
En savoir plusUn déviateur wye dirige le sucre soit sur 20 m vers le procédé humide pour la production de morceaux de sucre, soit sur 8,5 m vers la ligne d'emballage.
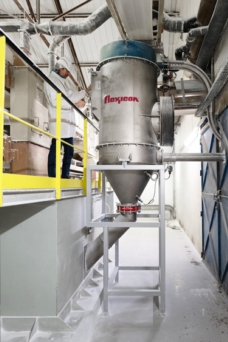
En savoir plus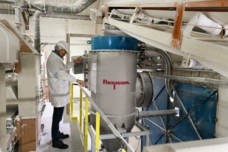
En savoir plusUn autre filtre séparateur reçoit le sucre et le déverse dans une trémie de réception qui alimente la ligne d'emballage. Tereos Sucre a choisi le transport pneumatique pour éliminer le risque de contamination.
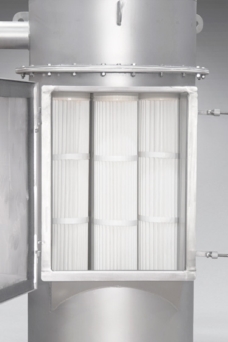
En savoir plusLe récepteur du filtre sépare le sucre du flux d'air à travers un média filtrant. Le nettoyage par jet d’air à impulsion inverse déloge les poussières accumulées pour une séparation continue des matières.
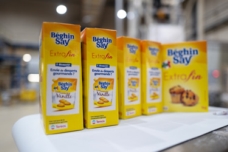
En savoir plusPaquets de sucre extra fin Tereos
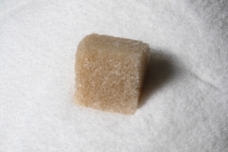
En savoir plusUn morceau de sucre de canne roux est placé sur un fond de sucre blanc extra-fin.