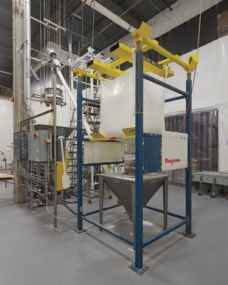
En savoir plusLa matière mélangée s'écoule d'un Big Bag dans la trémie d'un convoyeur à vis flexible, qui la transporte dans un séparateur vibrant alimentant une machine d'emballage.
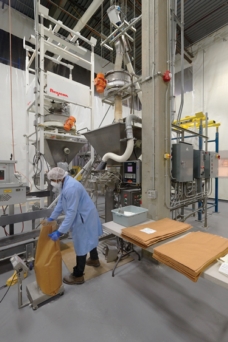
En savoir plusLe second déchargeur de Big Bags de l'entreprise, avec cribleur intégré dans le châssis, décharge les matières mélangées dans une trémie au-dessus d'une machine d'emballage.
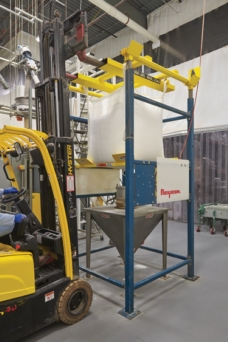
En savoir plus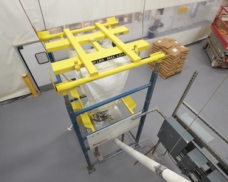
En savoir plusUn chariot élévateur place le Big Bag avec son cadre de levage sur le châssis du déchargeur Bulk-Out® BFF. Le mélange est transféré vers un convoyeur à vis flexible, un cribleur et enfin une ensacheuse.
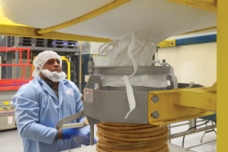
En savoir plusUn opérateur sécurise la goulotte du Big Bag avec un anneau de blocage Spout-Lock® positionné au-dessus d’un tube télescopique Tele-Tube® qui s’abaisse, la maintenant tendue pour améliorer le flux et la vidange complète tout en contenant la poussière.
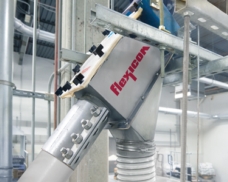
En savoir plusLes matières sortent du convoyeur en dessous du point où il est entraîné, ce qui empêche tout contact avec les joints ou les roulements.
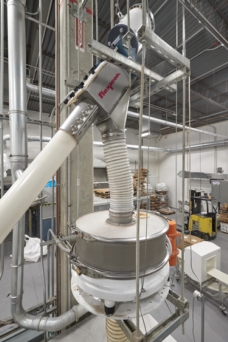
En savoir plusLa matière déchargée du convoyeur à vis flexible est criblée avant d'être acheminée vers une machine d'emballage.
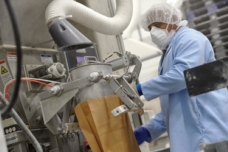
En savoir plus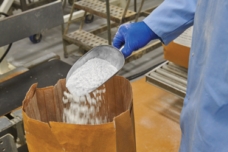
En savoir plusKB Ingredients emballe et expédie des mélanges aux industries de la boulangerie et de la transformation alimentaire.