
En savoir plus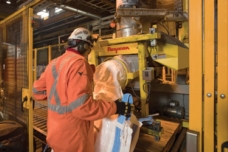
En savoir plusChaque remplisseur de big bags est équipé d'une tête de remplissage articulée Swing-Down, permettant à l'opérateur d'accéder en toute sécurité à tous les points de raccordement des sacs depuis le sol. Des pesons mesurent le gain de poids du big bag, permettant à l'automate programmable d'arrêter le cycle de remplissage lorsqu'il atteint le poids cible.
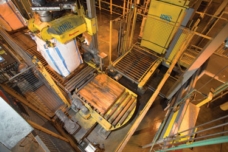
En savoir plus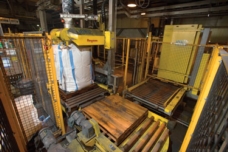
En savoir plusLe distributeur automatique de palettes (à droite) alimente le remplisseur de big bags qui reçoit les granulés de concentré de cuivre de la trémie d'alimentation d'une capacité de 11 tonnes située au-dessus.
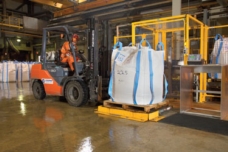
En savoir plus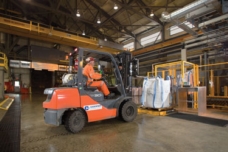
En savoir plus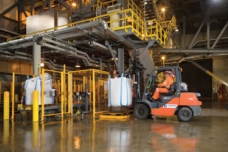
En savoir plusLe big bag rempli est retiré du compartiment de stockage à l'extrémité du convoyeur à rouleaux de 7,5 m de long.
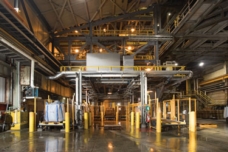
En savoir plus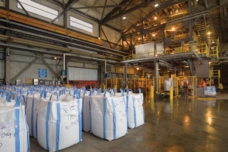
En savoir plusLe système automatisé de remplissage de big bag comprend deux remplisseurs (à l'arrière), un distributeur de palettes central et deux convoyeurs à rouleaux de 7,5 m de long à partir desquels un chariot élévateur dépose les sacs remplis en vue de leur expédition.
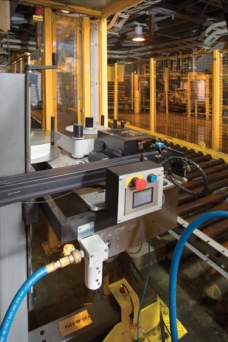
En savoir plusLes systèmes de distribution de palettes et de remplissage de big bags sont équipés de commandes automatisées, de systèmes de sécurité et de protections.