Un projet de manutention de produits en vrac à grande échelle dynamise la production d'aliments sans gluten dans une boulangerie
EAST HARTFORD, CONNECTICUT — Le gluten est une protéine que l'on trouve dans le blé, le seigle, l'orge et leurs variétés croisées et leurs dérivés. Le gluten est le liant de la farine qui empêche les produits de boulangerie et pâtisserie de s'émietter. L'absence de gluten, autrefois considérée comme un phénomène de mode, est en train de devenir une habitude alimentaire courante. En effet plus de 15 % des ménages nord-américains consomment des aliments sans gluten. Par conséquent, le marché des aliments sans gluten a doublé au cours des cinq dernières années et est maintenant estimé à environ 5,5 milliards de dollars.
Pour répondre à cette demande croissante, Bakery On Main, une boulangerie commerciale spécialisée dans les aliments sans gluten, avait besoin d'augmenter considérablement sa capacité. «Nous fonctionnions à 100 % de notre capacité. Notre équipement de manutention de produits en vrac, composé en grande partie de bandes transporteuses inclinées, était inefficace et très exigeant en main-d'œuvre», explique Michael Smulders, propriétaire de Bakery On Main. «C'était aussi un système ouvert, donc les ingrédients étaient exposés à l'air ambient».
Après avoir étudié diverses façons d'améliorer l'équipement existant, qui se sont toutes révélées insatisfaisantes, Smulders a décidé de construire une toute nouvelle installation dotée d'un système intégré de manutention en de matière vrac conçu spécialement pour les produits de boulangerie et de pâtisserie sans gluten. Il a chargé une firme d'ingénierie indépendante de s'occuper de la conception dans son ensemble. Le cabinet a travaillé en étroite collaboration avec la division d'ingénierie de Flexicon, pour créer un système entièrement intégré basé sur le système de convoyeur à disques FLEXI-DISC™ de l'entreprise.
Principe de fonctionnement d'un convoyeur à disques
À l'intérieur du système de convoyage à disques, une série de disques en polymère à faible frottement fixés à un câble en acier inoxydable fait glisser doucement les matériaux en vrac à travers des tubes lisses en acier inoxydable. Grâce à son action de convoyage en douceur et à son fonctionnement étanche à la poussière, un système de convoyage à disques est idéal pour le transfert de produits alimentaires fragiles et sensibles à la contamination.
Le tube en acier inoxydable peut être positionné horizontalement, verticalement ou à n'importe quel angle. Le système étant modulable, des entrées et des sorties peuvent être ajoutées au besoin pour contrôler le flux du matériau. Le système peut également être allongé ou raccourci pour s'adapter à l'espace disponible.
Quelle que soit la configuration, les disques et câbles en polymère à faible frottement sont entraînés par un rotor à une extrémité du circuit et maintenus sous tension par une roue d'entraînement à l'autre extrémité.
Deux systèmes intégrés produisent du granola et des flocons d'avoine
Bakery On Main offre cinq saveurs de granola sans gluten, y compris canneberge orange noix de cajou et banane noix tropical. La boulangerie offre également six saveurs de flocons d'avoine instantanés, y compris le Scone aux myrtilles et le muffin à l'érable et aux noix.
Le nouveau bâtiment s'étend sur 10 200 m2 et une hauteur de plafonds de 6,1 m. Puisque le granola et les flocons d'avoine exigent chacun un processus de production différent, Bakery On Main a recours à deux systèmes de manutention de matière vrac distincts de Flexicon dans son nouveau bâtiment.
L'intégration du système permet une production de granola entièrement automatisée
Le système de manutention de granola comprend deux circuits FLEXI-DISC TCC, un retourneur de caisses TIP-TITE®, un remplisseur de Big Bags TWIN-CENTERPOST™ et deux Vidangeur de GRVS BULK-OUT®.
Les principaux ingrédients du granola sont déchargés de extrudeur et versés dans le remplisseur de Big Bags, qui est équipé d'un joint gonflable et d'un capteur et d'un indicateur de niveau élevé. Les poteaux de rallonge réglables peuvent recevoir des Big Bags d'une hauteur de 2 300 mm lorsqu'ils sont pleins. Cette capacité d'ajustement est nécessaire car les matériaux à faible densité, comme ceux utilisés pour produire du granola, occupent plus d'espace par kilogramme.
Les sacs mis en palettes sont ensuite transportés par chariot élévateur vers un double système de déchargement de Big Bag qui se compose de deux stations de vidange BULK-OUT® identiques de la série BFC, chacune équipée d'une poutre en porte-à-faux en «I», un palan électrique et un chariot de levage pour le chargement et le déchargement des Big Bags.
Au niveau de chaque station de vidange de Big Bags, les principaux ingrédients du granola s'écoulent sur un alimentateur vibrant, passent à travers un déversoir réglable et sont versés dans l'adaptateur d'entrée non mesurée d'un convoyeur à disques de 150 mm de diamètre et de 30,6 m de long, doté d'une section verticale et de deux sections horizontales. Le déversoir est programmée pour ajuster la vitesse d'alimentation en fonction de la masse volumique en vrac du matériau.
Les deux stations de vidange sont montées sur des pesons qui mesurent la perte de poids et signalent aux alimentateurs vibrants de s'arrêter lorsqu'un certain poids préprogrammé a été transféré de la station de vidange au mélangeur (acheté séparément par Bakery On Main).
Les ingrédients secondaires sont déposés manuellement dans une petite trémie en raison de la nécessité d'une plus grande précision, et introduits dans le convoyeur à disques par l'intermédiaire d'un adaptateur d'entrée mesurée. Les ingrédients combinés sont ensuite déchargés du convoyeur à disque par l'intermédiaire d'un adaptateur de déchargement en ligne à flux complet et introduits dans le mélangeur.
Une fois bien mélangés, les ingrédients sont introduits dans un four qui dépose les produits cuits sur une bande transporteuse en mouvement. Le granola cuit au four est ensuite déchargé dans la trémie tampon d'un alimentateur vibrant qui achemine le matériau vers l'adaptateur d'entrée non mesurée d'un convoyeur à disques de 100 mm de diamètre, et 52 m de longueur.
Le convoyeur à disques décharge le produit fini par des vannes de déchargement tubulaires en ligne dans deux machines d'emballage équipées de capteurs de niveau qui signalent à un automate programmable de maintenir les niveaux de remplissage de la trémie tampon en démarrant et en arrêtant le convoyeur. Tout excès de granola est déchargé par l'adaptateur de déchargement des roues d'entraînement du système dans des caisses ouvertes, qui sont transportées par chariot élévateur jusqu'à un retourneur de caisses Flexicon TIP-TITE® situé à l'extrémité d'entrée du convoyeur à disques. Les caisses sont soulevées hydrauliquement pour créer un joint étanche à la poussière avec la hotte de déchargement. Celle-ci pivote ensuite pour se raccorder à l'adaptateur d'entrée non mesurée du convoyeur muni d'un joint d'étanchéité, pour le re-convoyage du matériel vers les machines d'emballage.
Le processus de production de flocons d'avoine est également entièrement automatisé
Le processus de fabrication des flocons d'avoine est également entièrement automatisé, bien qu'il ne nécessite ni cuisson ni ajout d'ingrédients secondaires. Reçus dans des Big Bags de 907 kg , tous les ingrédients sont vidés par un vidangeur de GRVS BULK-OUT® de la série BFC équipé d'un palan électrique et d'un chariot de levage pouvant contenir des sacs allant jusqu'à 1,62 m de hauteur.
Le contenu est déchargé sur un alimentateur vibrant puis est dirigé vers un adaptateur d'entrée non mesurée de 100 mm de diamètre et 11 m de longueur qui, à son tour, fait passer le matériau dans un adaptateur de déchargement en ligne à plein débit puis le déverse dans un autre mélangeur acheté séparément. Les ingrédients mélangés sont ensuite acheminés par vis sans fin vers une machine d'emballage.
Un deuxième circuit de convoyeur à disques de 100 mm de diamètre et 8,4 m de longueur, alimenté par un retourneur de caisses TIP-TITE, une trémie et un alimentateur vibrant, alimente une deuxième machine d'emballage.
L'étroite collaboration avec la société d'ingénierie a permis d'éliminer les obstacles
Tout au long de la conception, de l'ingénierie et de l'installation de ce système totalement automatisé et intégré, une équipe d'ingénieurs de la division ingénierie de Flexicon a travaillé en étroite collaboration avec la firme d'ingénierie indépendante mandatée par Bakery On Main pour s'occuper de la conception dans son ensemble. «Les collaborateurs de Flexicon ont apporté beaucoup de soin aux details», raconte Smulders. «Ils disposaient de toutes les ressources d'ingénierie nécessaires pour adapter le système à nos besoins exacts, y compris la suspension au plafond de tout les éléments, à l'exception des remplisseurs et des stations de vidange, afin de minimiser notre besoin d'espace. Ils étaient réactifs et notre collaboration avec eux a été très agreeable».
«La nouvelle installation nous permet d'atteindre la capacité accrue que nous visions sans augmenter notre effectif», explique M. Smulders. «Il faut maintenant moins de temps pour produire un lot. Les nouveaux systèmes réduisent les dommages aux ingrédients et sont beaucoup plus faciles d'utilisation pour les opérateurs. En outre, parce que les nouveaux systèmes sont fermés, les ingrédients sont beaucoup moins en contact avec l'atmosphère».
Smulders prévoit que le besoin de capacité de l'entreprise continue à croître au fur et à mesure que le marché des aliments sans gluten grandit. «Avec les lignes de production et l'équipe que nous avons mis en place, nous n'anticipons aucun problème pour répondre à la demande future», dit-il.
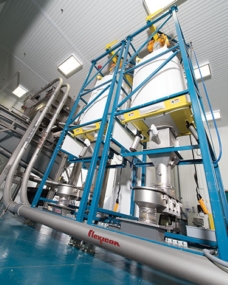
En savoir plus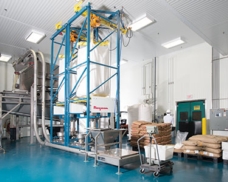
En savoir plusCircuit de convoyage à disques du granola Les ingrédients secondaires sont ajoutés manuellement par la trémie à droite tandis que les ingrédients principaux sont mesurés à partir de deux stations de vidange de Big Bags et versés dans le convoyeur à disques qui, lui-même, alimente le mélangeur (arrière plan).
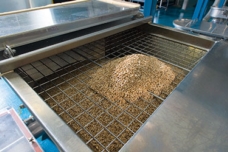
En savoir plus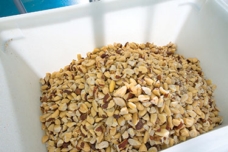
En savoir plusLes ingrédients secondaires du granola sont ajoutés manuellement à une trémie puis sont déchargés dans un adaptateur d'entrée mesurée et, enfin, rejoignent la ligne de convoyage à disques.
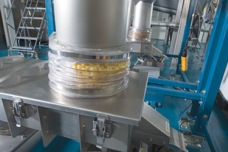
En savoir plus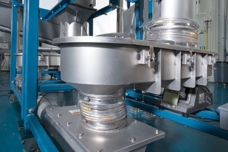
En savoir plusLes principaux ingrédients du granola entrent dans la ligne de convoyage à disques à partir des stations de vidange de Big Bags par le biais d'alimentateurs vibrants.
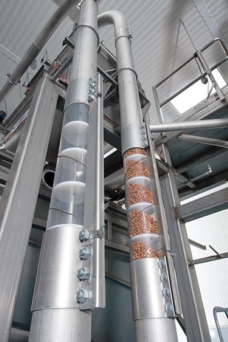
En savoir plusLa section transparente du circuit de convoyage à disques permet aux opérateurs d'observer les performances du système et le niveau de remplissage des «poches».
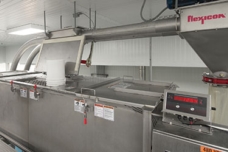
En savoir plusLes ingrédients du granola s'écoulent de la ligne de convoyage à disques dans le mélangeur en passant par un adaptateur de déchargement à plein débit .
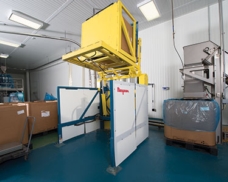
En savoir plusLe retourneur de caisses TIP-TITE® dépose le contenu des caisses de granola en excès dans la ligne de convoyage à disques qui les achemine vers les machines d'emballage.
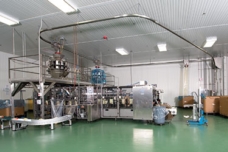
En savoir plus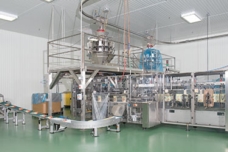
En savoir plusLe deuxième circuit de convoyage à disques alimente les trémies tampon de deux machines d'emballage de granola par l'intermédiaire de vannes de déchargement tubulaires en ligne.
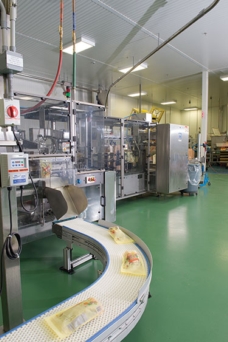
En savoir plusLes paquets de granola sortent de la machine d'emballage.
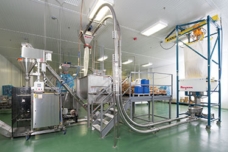
En savoir plusDans le premier circuit de convoyage à disques de flocons d'avoine, les ingrédients de la station de vidange de Big Bags en porte-à-faux sortent par un adaptateur de déchargement en ligne à plein débit et sont versés dans le mélangeur situé en dessous. Un convoyeur à vis incliné déplace les ingrédients mélangés vers une machine d'emballage (à gauche).
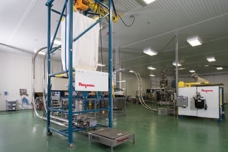
En savoir plusLa première ligne de convoyage à disques de flocons d'avoine, alimentée par une station de vidange de Big Bags, apparaît au premier plan. La deuxième ligne de convoyage à disques de flocons d'avoine, alimentée par un retourneur de caisses TIP-TITE®, apparaît à l'arrière-plan.
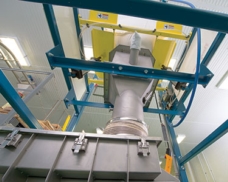
En savoir plus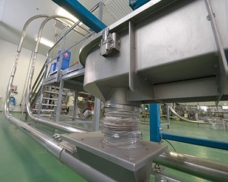
En savoir plusLes ingrédients destinés à la fabrication des flocons d'avoine descendent de la station de vidange de Big Bags et passent par un déversoir et un alimentateur vibrant avant d'être déversés dans la vanne d'entrée du circuit de convoyeur à disques pour être acheminés vers le mélangeur.
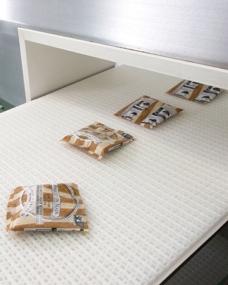
En savoir plusEmballages finis de flocons d'avoine
DD-0367