Un fabricant de confiserie norvégien améliore la sécurité, empêche la poussière et décharge automatiquement les Big Bags
TRONDHEIM, NORVEGE — Nidar AS, premier fournisseur norvégien de confiserie, fabrique 150 produits sous 35 marques sur 10 lignes de production. Son usine a été construite en 1950 et est mise à jour régulièrement avec des équipements modernes de manutention de produits vrac afin d'améliorer la productivité et l'environnement de travail.
En fait, l'usine à cinq niveaux (quatre étages plus le sous-sol) a été agrandie six fois pour répondre à la demande croissante, explique Tor Ove Kvingedal, l'un des trois ingénieurs de maintenance. «Mais comme pour la plupart des vieux bâtiments», dit-il, «l'agencement original n'était pas toujours optimal pour la production modern».
Lorsque l'alimentation par gravité n'est pas possible, l'usine transfère les matériaux en vrac à l'aide de stations de vidange de Big Bags, de convoyeurs à vis flexibles, de vis sans fin rigides et de convoyeurs pneumatiques — un équipement qui réduit le travail manuel, retient la poussière et s'insère dans des espaces très étroits, comme l'a démontré récemment l'ajout d'une station de vidange de Big Bags à deux demi-cadres.
Les stations de vidange de Big Bags permettent de réduire la main-d'œuvre et les émanations de poussière
Les ingrédients tels que le lait en poudre, le sucre, l'amidon et la poudre d'enrobage acide arrivent dans des Big Bags de 1,1 tonne. Nidar utilise un certain nombre de stations de vidange de Big Bags, dont six fournies par Flexicon Europe Ltd, pour les décharger.
La plus récente des stations de vidange de Big Bags est une unité à deux demi-cadres, qui traite deux types d'amidon dans un espace restreint au quatrième étage de l'usine.
Auparavant, l'amidon était acheté dans des sacs de 25 kg que les opérateurs transportaient du troisième étage au quatrième étage où il était déversé dans deux grands récipients, chacun pouvant contenir 200-300 kg. Comme le processus consomme 100 kg/heure d'amidon, 32 sacs étaient manipulés manuellement par journée de travail de huit heures. «Les opérateurs montaient les escaliers plusieurs fois par jour pour garder les cuves remplies», dit M. Kvingedal.
En plus du travail acharné, le déchargement manuel des sacs d'amidon était un processus générant beaucoup de poussière, dit M. Kvingedal: «La poussière d'amidon n'est pas nocive, mais désagréable et peut être très collante».
La nouvelle station de vidange de Big Bags à deux demi-cadres BULK-OUT® BFH-C-X, également de Flexicon, peut recevoir deux Big Bags côte à côte, fournissant suffisamment d'amidon pour permettre à la ligne de fonctionner pendant deux jours ou plus. «Le système réduit également l'effort manuel, retient la poussière et améliore l'environnement de travail», dit M. Kvingedal.
La station de vidange à deux demi-cadres permet de s'adapter à des espace horizontaux et verticaux
À l'origine, la poudre d'amidon s'écoulait par gravité à partir des deux grandes cuves du quatrième étage, à travers une paire de robinets-vannes à guillotine et des goulottes en acier de 150 mm de diamètre menant au troisième étage.
Les grosses cuves ne pouvaient pas être simplement remplacées par deux stations de vidange de Big Bags parce que la distance entre les sorties de déchargement aurait dépassé la distance entre les goulottes existantes, ce qui aurait nécessité de nouveaux trous dans le quatrième étage et le déplacement des goulottes.
La hauteur sous plafond de seulement 4,5 m posait également problème, car une hauteur libre insuffisante au-dessus des unités empêchait le chargement et le retrait des Big Bags à l'aide d'un chariot élévateur.
Pour surmonter ces deux problèmes, on a installé une station de vidange de Big Bags de 1,2 m de haut, à deux demi-cadres, qui peut accueillir deux Big Bags côte à côte. L'unité deux-en-un décharge par deux sorties suffisamment espacées pour éviter le déplacement des robinets-vannes à guillotine et des goulottes, tandis que le design à profil bas permet de suspendre les Big Bags à partir d'un palan, ce qui permet d'économiser 10 cm supplémentaires de hauteur sous plafond. «C'était très étroit», raconte M. Kvingedal.
Il a été facile d'enlever les réservoirs d'origine et d'installer la station de vidange de Big Bags à deux demi-cadres au-dessus des goulottes. Nidar avait simplement besoin d'une alimentation en air comprimé pour alimenter l'unité. M. Kvingedal raconte, «Nous avons installé la station de vidange de Big Bag en deux jours en novembre 2011. Une compagnie locale a fourni le palan. Il était essentiel que l'équipement soit installé rapidement, car l'amidon est un ingrédient clé sur cette ligne de production».
Économie de main-d'œuvre et réduction de la poussière
Une fois qu'un sac est mis en position, un opérateur tire la manchette du sac sur un collier de serrage SPOUT-LOCK™, ce qui crée une connexion sûre et hermétique à la poussière entre le côté propre de la manchette du sac et le côté propre d'un tube télescopique TELE-TUBE™. Au fur et à mesure que le sac se vide et s'allonge, le tube télescopique maintient une tension constante vers le bas, favorisant ainsi un déchargement complet.
Les activateurs de sac FLOW-FLEXER™ favorisent en outre l'écoulement à travers la manchette en soulevant les côtés inférieurs opposés du sac de sorte à lui donner un forme de «V».
Nidar a envisagé d'installer des ventilateurs de tirage, mais a décidé qu'ils n'étaient pas nécessaires, car la poussière était retenue par l'interface de manchette de sac de la station de vidange de Big Bags.
Après la descente à travers le tube télescopique, l'amidon passe à travers le robinet-vanne à guillotine, puis à travers l'une des deux goulottes verticales jusqu'à une station de pesage située au deuxième étage. Une vis à orientation horizontale de 170 mm de diamètre au troisième étage peut fonctionner dans les deux sens, de sorte que chaque station de vidange peut alimenter l'une ou l'autre des deux stations de pesage, qui envoient des signaux d'ouverture ou de fermeture des robinets-vannes à guillotine pour réguler le débit des Big Bags.
«Maintenir propre la station de vidange de Big Bags à deux demi-cadre est facile, il suffit d'utiliser des jets d'air comprimé ou un chiffon humide, et elle requiert peut d'entretien», dit M. Kvingedal. «Je n'ai aucun problème avec la station de vidange de Big Bags à deux demi-cadres».
Les bonbons qui plaisent aux norvégiens
«Toute nation digne de ce nom a sa propre chocolaterie et ses propres produits chocolatiers traditionnels», note le site Web de Nidar. Arborant fièrement le drapeau norvégien depuis sa fondation en 1912, Nidar est sans aucun doute une institution dans le pays.
L’entreprise développe et fabrique ses produits dans la ville de Trondheim (anciennement Nidaros) sur un site de 40 000 m2 qui comprend des machines de production, des bureaux et des entrepôts. L’usine emploie 350 personnes, dont 250 opérateurs. La production annuelle dépasse les 14 000 tonnes métriques.
L'entreprise produit des tablettes de chocolat, des boîtes de chocolats, des pâtes d'amandes, des bonbons gélifiés, des caramels, des produits à base de réglisse et des pastilles sous plusieurs marques historiques. Bien que la plupart des produits de Nidar soient reconnus partout, les Norvégiens ont des préférences historiques en matière de confiserie. L'un d'entre elles est la pâte d'amande, un ingrédient essentiel lors des célébrations de Noël et de Pâques. Une autre spécialité que l'entreprise exporte également vers la Finlande est la salmiak — la réglisse aromatisée au chlorure d'ammonium, ce qui lui donne un goût salé et paralysant pour la langue.
«Nous prenons plaisir à toujours innover en proposant différents types d'emballages», dit M. Kvingedal. «Mais lancer de nouvelles marques est plus difficile. Les norvégiens aiment leurs bonnes vieilles tablettes de chocolat et bon nombre de nos marques les plus populaires remontent à avant la Seconde Guerre mondiale».
Une nouveauté assez récente et très populaire est une barre chocolatée appelée Smash. Une approche moderne sur le thème du sucré-salé, Smash combine le chocolat au lait avec une collation à base de maïs salé.
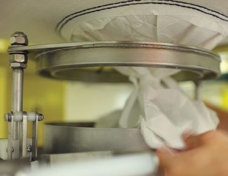
En savoir plus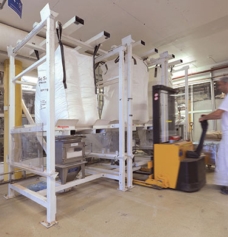
En savoir plus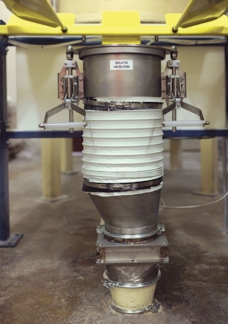
En savoir plusLes ingrédients tels que le lait en poudre, le sucre, l'amidon et la poudre d'enrobage acide arrivent dans des Big Bags de 1,1 tonnes, et sont acheminés par gravité vers les lignes de traitement lorsque cela est possible.
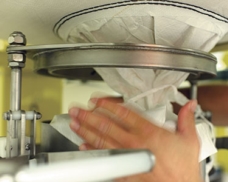
En savoir plus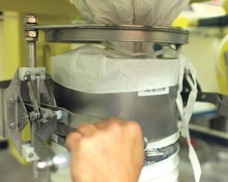
En savoir plusUne fois qu'un sac est mis en position, un opérateur tire la manchette du sac sur un collier de serrage SPOUT-LOCK™, ce qui crée une connexion sûre et hermétique à la poussière entre le côté propre de la manchette du sac et le côté propre d'un tube télescopique TELE-TUBE™, qui maintient une tension constante vers le bas pour favoriser un déchargement complet.
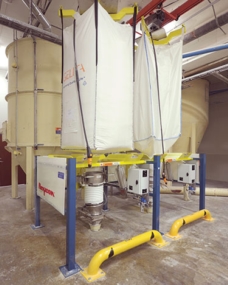
En savoir plus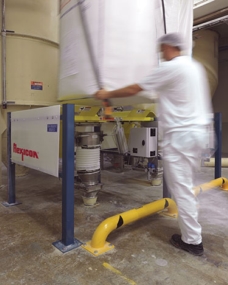
En savoir plusNidar AS a ajouté deux stations de vidange de Big Bags de Flexicon pour manipuler deux types d'amidon dans un espace restreint au quatrième étage de l'usine.
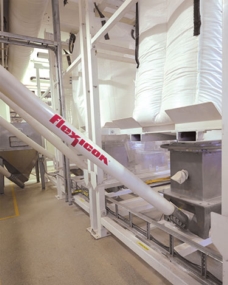
En savoir plusLorsque l'alimentation par gravité n'est pas possible, l'usine transfère les matériaux en vrac à l'aide de stations de vidange de Big Bags, de convoyeurs à vis flexibles, de vis sans fin rigides et de convoyeurs pneumatiques.
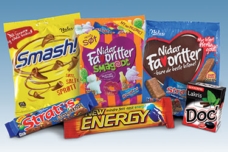
En savoir plusLe premier fournisseur norvégien de bonbons et confiserie fabrique 140 produits sous 35 marques, y compris ses nouveaux bonbons sucrés-salés Smash.
AA-0899