Le système de déchargement de Big Bag améliore la productivité et la propreté des opérations d’emballage
ATLANTA, GA — GSC Packaging exploite une installation de conditionnement sous contrat à la pointe de la technologie, produisant des sachets, des bâtonnets, des enveloppes et d’autres contenants souples pour l’emballage de produits alimentaires et de compléments nutritionnels. L’ensemble de l’installation est certifié Cgmp (certifié Good Manufacturing Practice) conforme par la NSF (National Sanitation Foundation), et certifié biologique et OU (Orthodox Union) Kosher. Le suivi des codes de lot et le contrôle des stocks en temps réel sont utilisés pour la multitude de travaux que l’usine traite chaque semaine.
Au service de clients prestigieux tels qu’Unilever, McCormick Spices, Ghirardelli et d’autres distributeurs de produits alimentaires bien connus, la société est spécialisée dans les poudres alimentaire sèche, y compris les assaisonnements, les suppléments protéiques, les mélanges pour boulangerie, les mélanges pour boissons, les mélanges pour soupes et les mélanges de céréales chaudes. GSC Packaging est également expérimenté dans les produits à ingrédients multiples tels que les mélanges de riz et de pâtes alimentaires où les divers composants doivent être déposés séparément dans un sachet.
L’usine a récemment amélioré sa productivité en mettant à niveau son système de manutention des produits en vrac avec ses machines d’emballage automatisées tout en améliorant la propreté de l’usine.
GSC reçoit des expéditions en vrac de produits alimentaires en poudre sèche dans des Big Bags de 227 kg et reconditionne le contenu dans des contenants flexibles individuels, que l’entreprise imprime et forme en interne à partir de rouleaux.
«Jusqu’à récemment, les Big Bags étaient suspendus dans un appareil stationnaire et vidés manuellement», explique Robert Shapiro, président de GSC Packaging. «Cela rendait difficile le maintien des normes d’hygiène appropriées. De plus, les poudres fines telles que les mélanges pour gâteaux et boissons ont généré de la poussière qui devenait un danger potentiel au sein de l’usine. Le processus manuel était également lent, devenant un frein pour les équipements de remplissage des emballages hautement automatisés.»
Pour accélérer la manipulation des sacs lourds, améliorer l’assainissement et éliminer la poussière, GSC Packaging a installé des déchargeurs de Big Bags automatisés alimentant les convoyeurs à vis flexibles Flexicon — le tout sous contrôle PLC. Les poudres restent totalement enfermées du Big Bags à la machine de conditionnement.
«La vitesse à laquelle nous pouvons vider un big bag n’est désormais limitée que par le taux de remplissage des sachets souples vers lesquels le contenu est transféré», explique Shapiro.
«L’ensemble du système est tellement automatisé et fiable que l’opérateur est libre d’assumer d’autres tâches.»
Les déchargeurs de big bags réduisent le travail manuel
Parmi les déchargeurs de big bags Flexicon se trouve un modèle chargé par chariot élévateur, avec une trémie en acier inoxydable finition sanitaire. Un opérateur de chariot élévateur attache les sangles du big bag à un cadre de levage et charge celui-ci dans le chassis du déchargeur. Une fois le cadre installé, l'opérateur connecte la goulotte du sac à l'entrée d'un crible vibrant circulaire qui décharge les poudres de taille standard dans la trémie au sol d'une capacité de 0,51 m3.
Les convoyeurs à vis flexibles alimentent les machines d'emballage
Pour accueillir les matériaux semi-fluides de GSC, les convoyeurs à vis flexibles de 4,6 m de long sont conçus pour déplacer les matériaux difficiles à manipuler. Constitué d'une vis tournant dans un tube en plastique flexible de 11,4 cm de diamètre extérieur, le convoyeur s'étend de la sortie de la trémie à une inclinaison de 45 degrés jusqu’à l'entrée de la machine d'emballage située à 2,7 m au-dessus du sol. La vis sans fin, actionnée par un moteur électrique à l'extrémité de décharge, alimente automatiquement le matériau dans la trémie de la machine d'emballage.
«Nous avons fourni des échantillons des divers matériaux en poudre que nous reconditionnons à Flexicon pour les tester», explique Shapiro. «Ils ont pu trouver l'une de leurs configurations standard qui pouvait les gérer toutes, ce qui est très important pour notre entreprise car nous ne travaillons pas avec un seul matériau tout le temps.»
La machine d'emballage dose le matériau en poudre dans des sachets souples de différentes tailles et capacités. Des capteurs de niveau haut et bas dans la trémie de la machine d'emballage envoient des signaux au PLC (contrôleur logique programmable) pour activer et désactiver le convoyeur lorsque le contenu atteint les niveaux maximum et minimum prédéfinis.
«Une fois que l'opérateur du chariot élévateur charge le big bag sur le châssis du déchargeur, connecte puis détache la goulotte du sac, le travail est pratiquement terminé», explique Shapiro. «La seule autre chose que l'opérateur doit faire est d'appuyer sur un bouton du panneau de commande pour démarrer le convoyeur, le PLC et les capteurs de niveau prennent le relais à partir de là.»
Les taux de remplissage des sachets souples varient. Il ajoute : «Il faut plus de temps pour remplir un sachet avec un mélange à gâteau léger et moelleux semblable à de la poudre que pour le remplir avec des particules plus grosses comme du riz ou des pâtes lyophilisées. Si les composants doivent être déposés séparément dans un sachet, cela augmente le temps de remplissage. Si nous vidons 1 à 2 kg par sachet, nous pouvons vider tout le big bag en seulement 15 minutes. Si nous ne vidons que quelques onces ou grammes par sachet, cela peut prendre plusieurs heures. Cependant, il ne faut que 3 minutes environ pour retirer un sac vide et le remplacer par un plein. »
Le convoyeur est conçu pour un fonctionnement conforme aux normes sanitaires
L'extrémité d'entrée du convoyeur à vis flexible ne nécessite aucun palier, et puisque l'extrémité de décharge est couplée à l'entraînement du moteur au-dessus du point de déchargement, le produit n'entre en contact avec aucun joint ni palier à l'intérieur du convoyeur.
Un capuchon de nettoyage amovible à l'extrémité d'entrée du convoyeur permet une vidange et un rinçage rapides du tube de celui-ci ainsi que le démontage et le lavage des composants. «Le système ne nécessite pas de nettoyage pour les petites séries», explique Shapiro. «Pour les longues séries, nous démontons et désinfectons le système au moins une fois par semaine.»
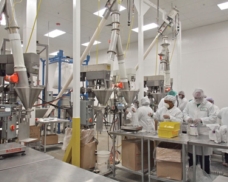
En savoir plusLes convoyeurs à vis flexibles alimentent automatiquement le matériau dans les trémies de la machine d'emballage.
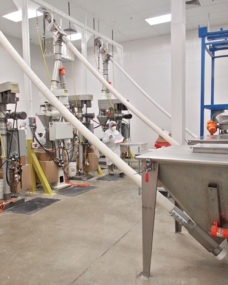
En savoir plusLes poudres restent totalement confinées, des Big Bags aux machines d'emballage, améliorant la propreté de l'usine.
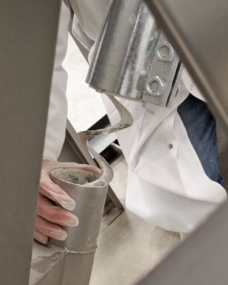
En savoir plus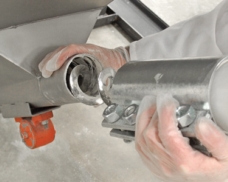
En savoir plusAprès avoir retiré le capuchon de nettoyage, un opérateur retire la vis flexible du tube du convoyeur pour un nettoyage en profondeur.
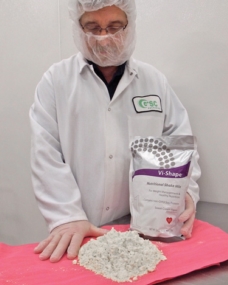
En savoir plusGSC Packaging reconditionne et remplit les sachets et autres contenants souples avec des produits alimentaires en poudre sèche et des compléments nutritionnels.
AA-0670